Key data helps effectively measure how successful your safety program is
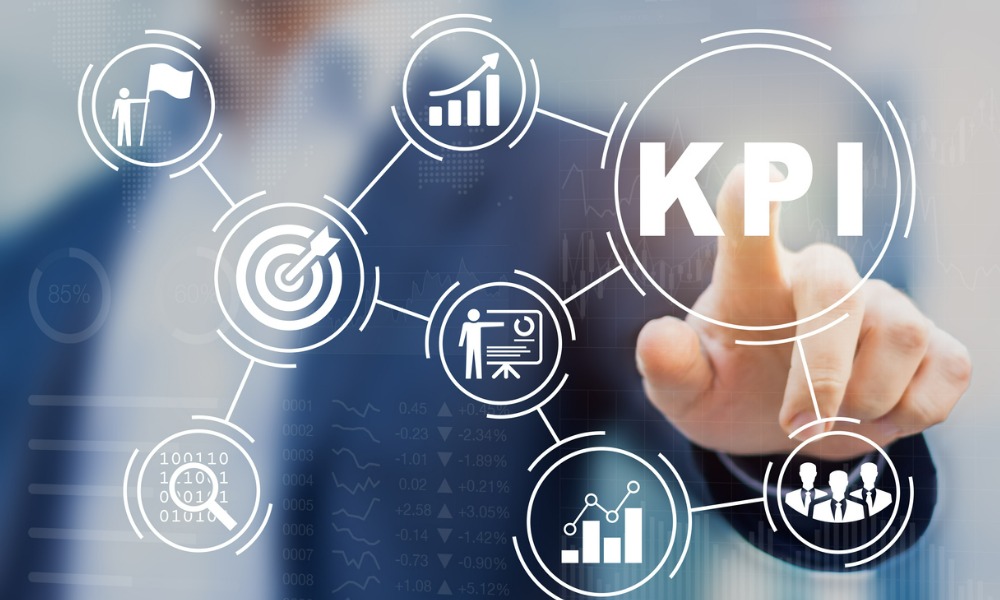
Safety data is essential in the way that it allows OHS professionals to assess, quantify and set goals around improving organizational health and safety. Safety Key Performance Indicators (KPIs) help track performance. They effectively measure how well your safety plan is doing. KPIs can also be used as a way to target and improve safety performance in certain areas of the business.
This data is typically split into two categories, lagging indicators and leading indicators. Lagging indicators are seen as more reactive, in the way that they examine the current state of affairs. They are most likely going to be things like accident reports. On the other end, leading indicators are seen as more proactive, because they can provide a future outlook on the safety performance of a company. Most organizations will typically use a mix of the two to get a fair outlook.
By no means exhaustive, here is a list of some of the most popular safety KPIs.
Reported incidents and accidents (accident rate). It is essential that all accidents and incidents are documented within the company. There are not only legal requirements about reporting, but accidents and incidents are one of the clearest indicators of whether a company’s safety program is effective (though human error will always exist, multiple injuries and fatalities will definitely be a sign of something amiss).
Lost time injury frequency rates (LTIFR). With this KPI, you can measure the frequency of incidents (or injuries) which occur over a period of time that caused lost time. Smaller injuries may not have a huge impact on lost time, but more serious ones could result in days or even weeks off – which can have a direct impact on the company’s bottom line.
Reported near misses. Sometimes workers may not feel the need to report near misses or tiny accidents, but it is important to track near misses because they still indicate a potential hazard – just because no one is injured doesn’t mean that the process can’t be improved.
Equipment breakdowns. If equipment is breaking down often, that’s not a great sign. It reduces productivity and more seriously can create potentially unsafe situations for the worker. Tracking this measures the effects that breakdowns (and maintenance) can have on both productivity and safety.
Average overtime hours per person. This is important to track because if a worker is frequently working overtime, they may end up becoming exhausted and more prone to errors or lapses of judgment – creating a potentially unsafe work environment.
Employee attendance rates. Similarly to the above point, tracking attendance rates helps keep track of worker health and safety. If someone is frequently missing work or calling sick, this could be the sign of a physical or mental ailment created by the workplace.
Training. Keeping track of worker and manager training is important for a number of reasons. Some types of training are mandatory, so safety professionals need to keep track of who has done what to ensure compliance. Separately, are additional safety programs being offered? And is this correlating which increased productivity or safety? This is something to be aware of.
Average time to resolution of risk/average resolution time (ART). Response time is important, because it can make the difference between life and death – with regards to first aid for example. You can put into place tech systems that can help you track the time it takes to resolve incidents from the minute they are reported, to see if you can improve those times.
Accident-free days. This measures this number of days in which no workplace accidents have occurred. Sometimes, it’s nice to include more positive indicators to celebrate success!
Audit/inspection scores. All external and internal scores should be tracked, they are a very basic way to see if there has been improvement over time. Conversely if there has been a dip over time, what can be done to improve.