Despite continued efforts, some companies are not experiencing the improvements so hoped for. There are a number of reasons for this and one of them is that our worker competency development programs are lacking
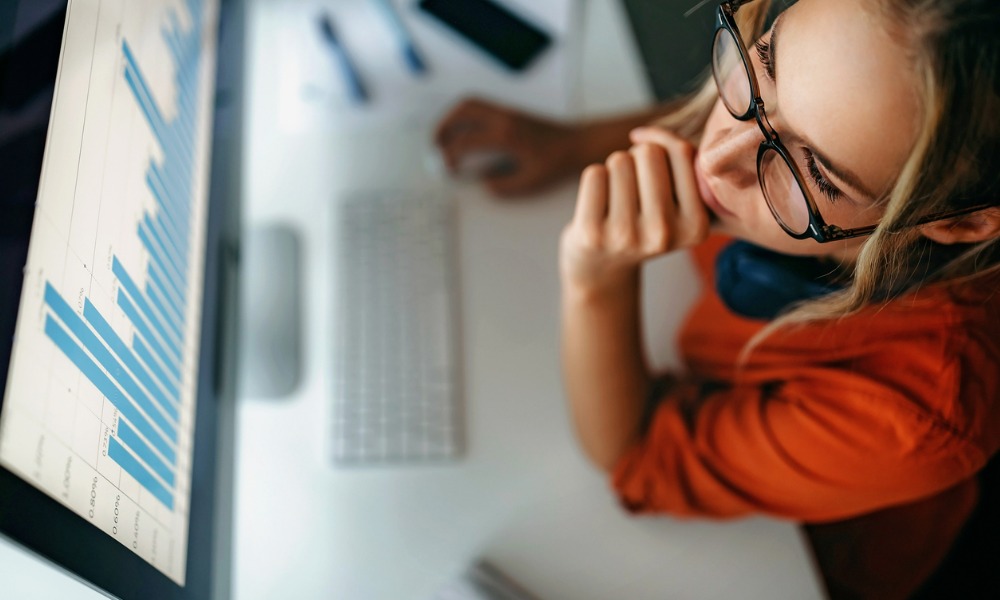
Continuous improvement is a key tenet of the Shewhart cycle, plan-do-check-act. Companies continue to make improvements to their occupational health and safety management systems (OHSMS). Companies continue to invest in safety, but the normalized worker fatality rate is not going down.
In an earlier column, I wrote about the need for employers to invest heavily in employee competency. Competency requires formal integration of education and training. Competency is not achieved by offering basic safety courses. Competency isn’t about hiring workers who have had a certain number of years of specific work experience. Competency development requires a specific energy, effort, and intention.
Competent employees have the education to know what they need to know to do their jobs safely. Competent employees have been trained to be able to do their jobs properly. Competency requires the development of knowledge and skills combined with certain other attributes. Education without training leads to sloppy work outcomes. Training without education creates an employee and workforce ill prepared to deal with unusual circumstances that can arise leading to uncontrolled risk. The education provides the theoretical underpinning to allow a properly trained employee to achieve safe production every day.
The design of work methods requires that the knowledge, skills, and attributes the worker must be able to do or perform are formally identified. The starting point is the development a job description and a competency profile. All positions identified on the organizational chart must be included. The competency profile needs to describe what a worker needs to know and what a worker needs to be able to do. Typically the competency profile includes elements such as:
- Industry-wide competencies such as safety legislation, safety awareness, quality control and continuous improvement.
- Industry—specific competencies such as drilling and completions, infrastructure construction and pipelining.
- Occupational-specific competencies such as crane operation, plant operation, or Class 1 driver’s license.
- Job-specific competencies such as cutting wood with a chain saw, lubricating equipment and general house keeping.
- Task-specific competencies such as starting a chainsaw, changing a bit on a drill and checking vessel pressure.
Read more: How to choose the best chainsaw pants for your logging and forestry team
In the context of safe work, a competent person is able to identify existing and predictable hazards in their surroundings. Just as importantly, they have the authority to take prompt and corrective measures to eliminate them. As an occupational health and safety consultant, I have investigated many serious and fatal incidents. Sadly, low worker competency has been a major factor in all of them. Quite simply, these employees did not see the hazards, nor did they understand the risks associated with exposure to these hazards. Their supervisors didn’t see the hazards either and so corrective actions were not taken to eliminate the risks that led to the serious injury or death.
Safe production is only achieved when a competent team works together. Education and training are important but in the context of most workplaces the three most relevant terms are qualified, certified or licensed, and authorized. The qualified employees have the education and experience and have successfully demonstrated the ability to solve or resolve problems related to a particular work or subject matter. The certified or licensed employees have passed an examination process. This may be a formal exam offered by an accredited organization or it may be an informal process such as employee passing an in-house exam. The authorized employee is the person on the job site accountable for the work operations and has been assigned by the employer to oversee and take ownership for the completion of work or specific duties at a specific location at a worksite. Safe production is the output of the competent team, and this has to be cultivated by the attitudes of the authorized person. The authorized person leads by example and must show a genuine concern for making sure everyone makes it home safely at the end of their shift.
The process of creating a competency framework can be a daunting task. Establish a list of the knowledge, skills and attributes needed for success. Ensure your work teams include qualified, certified, and authorized personnel. Establishing a competency framework will increase the level of understanding and the necessary linkages between individual roles and organizational performance, making the extra effort required well worthwhile.
Glyn Jones is a partner at EHS Partnerships Ltd. in Calgary. He is a consulting occupational health and safety professional with 35 years of experience. He also provides program design and instructional support to the University of New Brunswick’s OHS and Leadership Development certificate programs. He can be reached at [email protected] or you can follow him on Twitter at glynjones_ehsp.
This article originally appeared in the July/August 2021 issue of COS.