Subtleties in the organizational environment affect employee behaviour
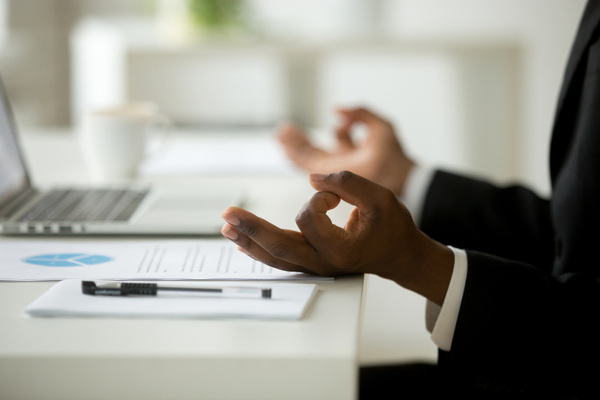
Having started in the business of safety back in 1994, I was part of a team building a safety management system from scratch and I was rewarded almost immediately by considerable improvements in our safety performance. But eventually, those improvements trailed off, and in some years our performance actually took a turn for the worse. As hard as we sliced and diced the numbers, the traditional metrics simply couldn’t explain why this should happen — and when you are personally standing before a board of directors looking for answers, not having one is never good.
So, in this vein of desperation, I was forced to look outside the existing science of safety, and quite by accident fell into the world of industrial/organizational psychology.
I stumbled upon one particular study (Brown et al, 2000) that was pivotal in broadening my own understanding of incident causation. In summary, this study offered the following insight:
“In modern industrial settings, the majority of incidents can be traced to substandard acts. Although the substandard act is performed by an individual, factors in both the operating and social environment either directly precipitate or influence the performance of that act.”
This statement is enlightening from several perspectives. Perhaps most notable is the recognition that people behave the way they do based in large measure on the environment they’re in. So, if the behaviour of our employees is leading them to accidents, doesn’t it logically follow we should be looking at the organizational environment to understand how it is being supportive of these negative behaviours?
Now, in the interests of full disclosure, I freely admit to being the proverbial blunt instrument in the shed. I was in no way a proponent of this piece of academia right out of the gate. First, I had to weigh the theory against what I did understand and that was our own organization’s experience. But once we looked at the data in context, the light bulbs were most definitely lit! What we found was an amazing correlation between an increase in negative safety performance with significant organizational change; with this correlation existing in the absence of any change in the traditional safety drivers within the safety management system itself.
Of course, no one in a position of leadership today would consciously contribute to an “unsafe” working environment but take a step back and examine the subtleties that exist in all organizations. Do we publicly reward the “Git ‘er done” team? Do we say, “No shortcuts, but we need to be back on line at 1600 hours”? Do we measure productivity, attainment and utilization, while classifying safety meetings as non-productive time? Do we encourage driving time to be also time spent in phone meetings? Do we assume technical competence defines overall competence? Do we burden the employees with so much personal protective equipment (PPE) and so many procedures that they physically can’t do their work as designed? Do we expect instant email responses at all hours? Do we encourage chronic fatigue by requiring herculean discretionary efforts? Do we respond to the bearers of bad news in the same way as those bringing good news? The list goes on and on, but it’s not a stretch to see how these influences can overwhelm the best of safety management systems.
The short answer then becomes that to expect a change in the safety behaviours (substandard acts) of employees in the absence of a change in the organizational environment that is actually driving those behaviours, is absolute madness. Unfortunately, this is exactly what we’ve been doing in the fervent hope things would improve.
Be that as it may, this is where the new opportunity arises. If the organizational environment contributes to negative safety performance, doesn’t it follow that the organizational environment can also contribute to positive safety performance? The difficulty of course is understanding what constructs create a positive organizational environment, and once identified, how to incorporate them into the organization’s way of being.
But difficult is not impossible and given the potential elimination of so many of the workplace tragedies we see every day, the redirection of resources away from the repetitive re-tweaking of the safety management system, seems like a no-brainer.
In our case, this was the challenge taken up by me and industrial psychologist Shelley Parker around 2012. Over the course of four years we researched existing literature in the fields of general social theory, management theory, high reliability organizational theory and motivational theory to identify those constructs common to organizations during periods of positive performance, especially with respect to safety. While we found dozens of potential constructs, we were able to isolate and assemble five into an organizational model: relatedness, competence, autonomy, upward dissent and mindfulness. This process naturally necessitated a specificity of definitions for each of the constructs, not only for the sake of clarity, but to ensure a smooth transition from academia into the world of industrial operations.
Once developed, the model’s integration into the organization was most certainly an interesting process but was accomplished using as many of the existing tools and processes as possible, so as not to be overly problematic and to avoid that feeling of foreignness. That is not to say there were not challenges — the status quo can be a difficult beast to budge and continuing to throw money at the problem in the creation of more and more administrative and engineering controls seems to somehow make us feel like we’re trying. That notwithstanding, we introduced the model slowly at all levels of the organization at the same time but did so use differing methodologies appropriate for each subset of the various employee groups. To say the least, we learned a lot along the way.
But the proof lies always with performance. Subsequent to the initial introduction of this model into our organization, we experienced the safest three consecutive years in our corporate history; especially notable as we had already been respected as a high performer from a safety perspective. In 2016, we were recognized by Canada’s Safest Employers Awards (presented by Canadian Occupational Safety) for having the best psychological safety program in the country, as well as the best overall safety culture.
One final point needs to be emphasized. This organizational model in no way replaces the safety management system. In the absence of the tools, policies, procedures, joint health and safety committees, PPE and audits, safety simply can’t happen. However, in order to be effective, the system must be consistently used by every participant in the workplace. In order to do that, we must shift our focus away from the provision of more “stuff” aimed at employees to a change in the working environment itself.
Incorporating these five simple constructs into your organization’s DNA will create the environment where the stated expectations of the organization actually align with the shop floor reality. That’s when safety just happens.
Duff Boyd retired as the director of health and safety for NB Power in 2018. Over the past 10 years he has been an outspoken advocate for shifting the focus away from presumed weaknesses in the safety management system to concentrate instead on the organizational influences on incident causation. He currently consults with both the private and public sectors as well as academia. He can be contacted at [email protected].