Questions must be specific, measurable, realistic
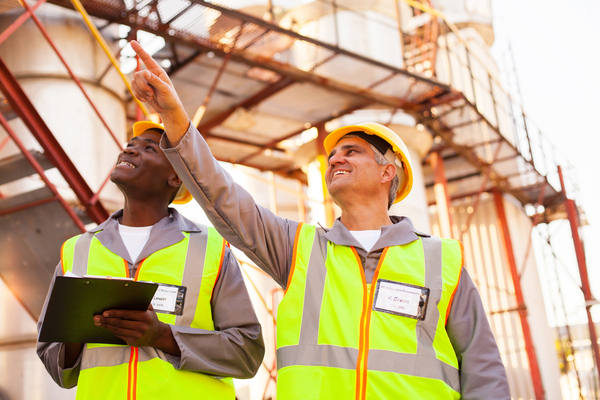
Throughout my career in health and safety I have promoted the idea of not necessarily adding new elements to your safety program but doing the existing elements effectively.
Workplace inspections are an essential, proactive part of an overall safety program that has been in place for decades.
Have you audited the effectiveness of your workplace inspection procedures (WPIs)? Do you have an audit tool that could measure WPI effectiveness? What critical points should be on the audit checklist?
Perhaps the biggest flaw in workplace inspection procedures is that the procedure does not clearly state the parameters of the inspection. Are you looking to measure compliance to safe work conditions, safe work practices or training requirements?
Most workplace inspection procedures do not differentiate between questions that should be on the checklist and questions that should be on bigger system audits. Questions relating to training should be left to bigger health and safety program audits.
Once the employer — in co-operation with the health and safety committee — has determined what the inspections are measuring, the next step is to identify the hazards and controls.
We know how important the preparation stage is in ensuring the quality of the WPI process.
A quick review of the preparation stage ensures that the following has occurred in the development of a quality workplace checklist for the area being inspected:
- Complete hazard mapping.
- Review of past workplace inspection and hazardous occurrence and near-miss reports.
- Complete job hazard analysis and the resulting safe work practices.
- Review of health and safety legislation and standards.
- Diagram of workplace layout.
- Inventory of equipment and chemicals.
It is important that your checklist is not generic. It must be specific to the rooms/buildings you are inspecting to be effective. It must be based on the results of the findings of the preparation stage above.
It is critical that the checklist questions be specific, measurable and realistic. Almost all checklists I have reviewed, even from safety sources, have questions in the checklist that are not measurable.
I can tell usually in less than a minute after looking at the checklist if it is weak or not. Questions that contain words like “appropriate,” “correctly,” “accordingly,” “regularly tested” and “adequate” are just a few examples of words that are not measurable and clearly point to a workplace inspection checklist in need of renewal. Too many times poor questions like “Is the employee wearing the appropriate gloves?” or “Is the spill kit is regularly maintained?” are seen on the checklist.
Oftentimes, there are no questions at all, simply three words, such as “Housekeeping is good." You must review and revise your workplace inspection procedures to improve the quality of the checklist.
Do the questions of your workplace inspection checklist reference the standard that the question was derived from. Remember, your checklist is the standard you are using to perform the checklist. It will reduce debate and conflict if your checklist identifies where the requirement for this question came from.
For example: “Is the emergency lighting illuminated, operable and checked monthly as per COSHR: 6.10(1)?”
The above question describes exactly what standard (in this case legislation) the checklist question comes from.
Are the hazards identified on the inspection report corrected in a timely fashion? It is the employer’s responsibility to ensure the hazards identified in the report are corrected. I like to use the role of the health and safety committee to check in on the system to ensure this element and others in the health and safety program are working effectively.
For workplace inspections, the non-compliances identified in the report are kept on the monthly meeting minutes until they are corrected. This ensures the employer is held accountable.
Perform an annual review of the workplace inspection element of the health and safety program. What are the types of questions you should be asking in your review to ensure your workplace inspection procedure is an effective, efficient and current part of your overall health and safety program?
Nothing is worse than having a checklist that is old and does not reflect the current hazards in the workplace. Ensure your checklist and procedure are reviewed at least yearly or if conditions in the workplace change.
How often are employees trained on how to perform a workplace inspection? Is workplace inspection training done online? It is important you set a standard for how frequently employee training and refresher training must occur. It is also important to realize that online training is not ideal for some elements of safety training. I feel strongly that a practical course on how to perform a workplace inspection is necessary.
How often is your workplace inspection element of your safety program audited by an outside party? It is important to have a set of fresh eyes look at your workplace inspection element and provide recommendations for improvement.
Before you start working on more elements of your health and safety program, look closely at your workplace inspection program and ensure it is in peak shape.
Paul Langan has been a national laboratory health and safety co-ordinator for 25 years. He can be reached at [email protected].