New CEO of Saskatchewan's Workers' Compensation Board explains the key areas of the province's strategy for tackling serious injuries and workplace deaths
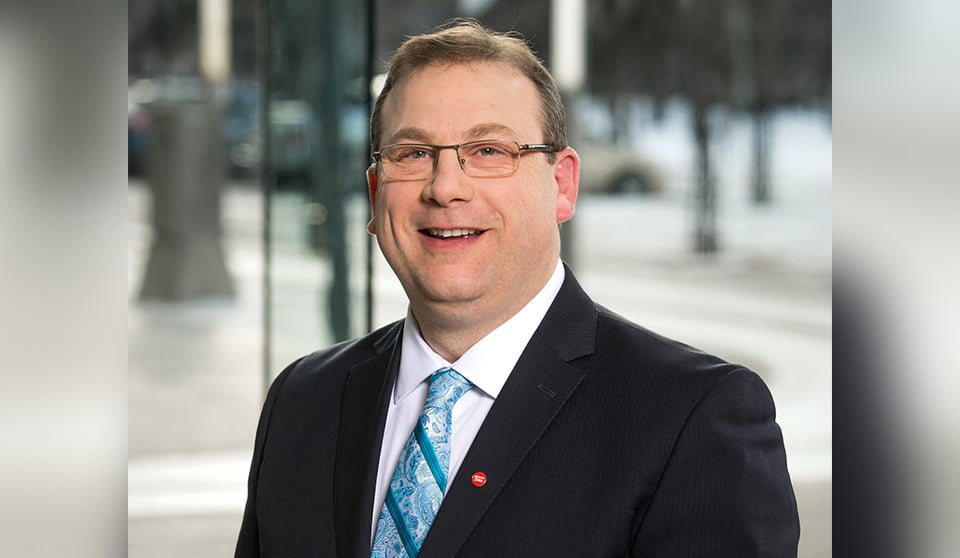
Late last year, Saskatchewan announced a new three-year strategy to reduce serious injuries and fatalities in the province. According to the Saskatchewan Workers’ Compensation Board (WCB), although the time loss and total injury rates have seen “a slow and steady decline” over the past decade, there are about 2,400 serious injuries annually, which has remained fairly flat. Additionally, from 2010 to 2018, the WCB accepted 354 work-related fatalities.
“We started to understand through analysis that it was the serious injuries and fatalities that weren’t going down,” says Phillip Germain, CEO of the WCB. “We said, ‘Here is what we are seeing; we think we should shift our focus from just all injuries to a greater focus on reducing serious injuries and fatalities.’ So, now, we needed to think about how do we transition from our current strategy into this new strategy.”
After meeting with various stakeholders over the past few years and tweaking the strategy as needed, the three-year plan ultimately focuses on four injury priority areas: asbestos exposure, work-related motor vehicle crashes, firefighter cancer exposure and falls from heights. The plan is spearheaded by WorkSafe Saskatchewan, a partnership between the Saskatchewan WCB and the Ministry of Labour Relations and Workplace Safety.
Asbestos exposure is the number 1 cause of workplace fatalities in Saskatchewan, according to data spanning from 2010 to 2018, accounting for 66 per cent of occupational disease fatalities during that time frame. While buildings and residential homes may no longer be made with asbestos, there is a flurry of renovation and demolition activities that risks exposing workers to the dangerous substance. Many of these new workers who are conducting these tasks likely don’t even know what asbestos looks like or where it can be found, says Germain.
“The ’40s through to the ’80s are what caused the reason why we are having so many asbestos exposure-related fatalities. People were exposed many years ago and now they are passing away because of this disease. We don’t want another bubble coming through in 20 years; we want to prevent it now.”
As part of the strategy, the province will continue to run its asbestos awareness campaign, form an industry best practices group to investigate the development of an industry standard as well as develop and improve communications regarding asbestos handling and disposal requirements.
Work-related motor vehicle crashes are the number 2 cause of workplace fatalities in Saskatchewan. WorkSafe has partnered with Saskatchewan Government Insurance (SGI and the Saskatchewan Trucking Association) to achieve its goal of reducing work-related motor vehicle crashes by 30 per cent by Dec. 31, 2021.
“They are helping us understand what’s driving these motor vehicle-related crashes and support organizations in figuring out what they can do to prevent these issues,” says Germain. “[We are] trying to make sure the companies that have lots of motor vehicles on the road and the workers themselves get the right information to manage these risks properly.”
The three-year strategy also signals the intention of developing a targeted field campaign with federal Occupational Health and Safety.
Firefighter cancer exposure is the third priority area identified in the strategy, accounting for 23 per cent of occupational disease fatalities between 2010 and 2018. It aims to improve firefighter cancer prevention controls by 50 per cent in Saskatchewan by Dec. 31, 2021. It outlines the intention to complete firefighter cancer audits and improve awareness to reduce the risk of future firefighter cancer exposures. It is also hoping to investigate the feasibility of a grant program to help with improving and purchasing additional hazard controls, such as particulate blocking hoods or backup sets of turnout gear.
“It’s one that we’re seeing trend up,” says Germain. “We are working with the fire halls and fire chiefs across the province and we are starting to understand some of the drivers of these cancers, what’s causing them.”
Some of the results were rather surprizing, including that it’s not just exposure to carcinogens while fighting a fire that are hazardous to the firefighters.
“Often, the most dangerous time isn’t during the fire; it could be after the fire when it’s still hot and it’s gassing off,” says Germain. “It could be the clothing that they’re wearing. If they don’t wash it right, they could be bathing in these chemicals because it’s soaked into their gloves and jackets and boots.”
Yet another example is exposure to diesel while conducting maintenance on the fire trucks.
Finally, the fourth priority area identified in the three-year strategy is falls from heights, something with which many industries grapple. WorkSafe is aiming to reduce falls from heights injuries by 30 per cent and develop or adopt an appropriate fall protection training standard with the help of an industry best practice group. One of the main challenges in this area — regardless of industry — is working off ladders.
“We were surprised by how many falls at heights were still happening off of ladder use,” says Germain. “It could be kind of a ‘back to the basics’ message around falls from heights.”
WorkSafe is also working with the residential construction industry to understand what its real challenges are in using fall protection and what can be done to educate or assist the industry.
“[Sometimes,] they don’t believe fall protection will help them or it costs them money in terms of it slows them down,” says Germain. “If they’re not able to be profitable based on a certain way of doing it, you now know why they are putting themselves at risk. But there’s got to be a way for them to be profitable and use fall protection — there has to be.”
Germain not only has experience working with the residential construction industry during his time with the Alberta Construction Safety Association early in his career but he intimately understands the challenges of small businesses because his mom was a janitor with her own contracting business and his dad was a small contractor.
“I understand how good people may not know anything about health and safety, but that doesn’t mean [that] because they don’t focus on health and safety they are not good people and they aren’t good companies,” says Germain. “I know from my own experience growing up [that] this wasn’t intuitive and it wasn’t easy.”
Return to work
It’s clear in speaking with Germain that he is quite passionate about helping injured workers return to work. According to WCB statistics, roughly 11 per cent of claims represent 80 per cent of costs and 80 per cent of comp days. Germain says he wants to determine what is unique about these claims in order to manage them effectively.
“How do we identify the determinants of these claims? What’s common about them and what is it we can do to assist?” he asks. “For sure, some of those people will need to be on long-term earnings replacement, they will never go back to work, but how many of those people if we [had] done the right thing at the right time could have and should have returned to work?”
Take, for example, a roofer who falls off a ladder and breaks his arm but does not go back to work after it has healed. The employer is upset, the WCB is confused and it’s the typical story you hear around those challenging claims.
“But what if what we have not realized is that [the] worker now has a phobia of heights, now he has a fear of falling and we didn’t identify it as [a] barrier — now there’s a psychological barrier that looks like the person is healed,” says Germain.
Fear of pain, fear of re-injury, low social network, substance abuse and mental health issues are just some of the determinants of what get in the way of people returning to work. Soft tissue injuries are a great example of this, says Germain. Two identical claims may come in, but it takes one person three years to heal and go back to work, while the other is back on the job in just six weeks.
“When we start to dig into it, we believe the difference is that other individual has some of those other determinants that we are not aware of,” he says. “So, what’s our process for identifying these determinants up front and instead of allowing the claim to get off track?… Are there things we could have done that would have prevented all of this from becoming a problem down the road?”
While he has been in his new role for less than a year, Germain has worked for the WCB since 2005, and he has a very clear idea of what he would like to have accomplished in his time at the organization: figure out how to effectively reduce serious injuries and fatalities, as well as manage them properly.
“It boils down to good customer service. How do we help these companies and injured workers deal with these issues?” says Germain. “I really believe there’s a win-win where, if we learn how to deal with these serious injuries more effectively, the employers will go ‘That’s great service for my injured worker’ and the injured workers are saying, ‘We were very well treated and supported at WCB.’”