Company wins gold in manufacturing category of Canada's Safest Employers awards
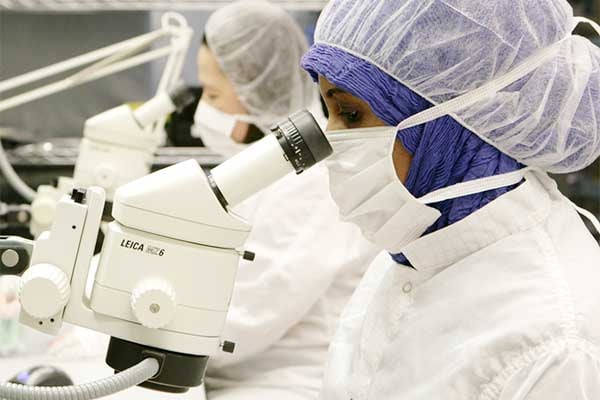
Ensuring the safety of production-line employees working shoulder to shoulder with large robots is one of many challenges that Celestica faces in its 1-million square foot electronics manufacturing facility in Toronto. With the constant influx of new products and programs requiring different manufacturing methods, Celestica’s proactive, progressive safety culture is a must.
“Our biggest challenge is continuous improvement,” says HR manager Gian Detta Colli. “We are always looking for better ways of working and keeping our people in safe hands.”
With customers in various markets such as aerospace, defence, energy and health care, Celestica faces diverse industry-specific safety issues that sometimes call for outside specialists to help devise programs. Detta Colli points out that senior leadership does not hesitate to invest in creating a safe environment for the company’s 1,800 employees in Canada.
Numerous management systems define responsibilities in all areas and detail the steps that need to be taken. When a new product is built, engineering manager Jean François Daigle and his team work with supervisors, managers, the joint health and safety committee (JHSC) and the health and safety department to conduct a risk assessment and put controls into place that eliminate or minimize risk.
“We have to manufacture the product to the customer’s specifications while taking into consideration the dangers around equipment, processes, chemicals and other aspects,” he says.
In aerospace and defence, for example, where cyanide is used in circuit boards, safety solutions include monitoring exposure to different levels of the chemical, ensuring proper ventilation and purchasing personal protective equipment.
Once new manufacturing equipment is operating or a program is in place, employees are encouraged to come forward if they feel unsafe or see an area they can improve. To that end, the company’s health and safety team has developed the Daily Safety Kaizen Continuous Improvement Program (part of Lean Six Sigma) and presents awards for contributions. The program includes forming a team to identify a safety issue, analyze it, document improvements on the Kaizen form and submit those to their supervisor or manager for approval.
Some suggestions have led to engineering solutions, such as designing a blocking mechanism for heat emanating from a process that made employees uncomfortable. Another prevented muscle strain by changing the configuration of a skid and platform holding large rolls of product. Other issues, such as increasing employee awareness about elevator safety, have led to posters and signs devised by the facilities and JHSC teams. Over the past year, ideas submitted and implemented have increased by 30 per cent, from 687 in 2015 to 908 in 2016.
According to facilities co-ordinator Rick Cyr, employee buy-in ensures that the safety program’s effectiveness is sustainable over the long term.
“Safety has to be both top-down and bottom-up, with everyone treating it as a critical issue,” he says. “Employees are well aware of processes and procedures, and by following them, they mitigate potential risks at the outset.”
Safety in manufacturing is complemented by other programs and initiatives to protect employees in whatever they do. These range from an annual wellness fair to a corporate TV channel that promotes health, safety and awareness. Communication vehicles include safety boards across the site, video screens that depict the safety tip of the month and an electronic news bulletin.
This article originally appeared in the October/November 2017 issue of COS.