But a workplace incident could have devastating consequences on 'family' culture
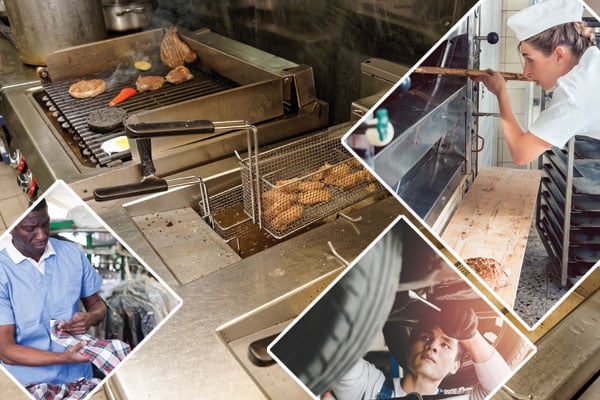
Sriram Rangan is in the business of safety. His Toronto-based company, Vagans, designs and manages safety programs for trucking companies of all types and sizes. His staff monitors log books of hazardous material carriers to make sure the drivers are not exceeding their hours. They ensure preventive maintenance is completed for refrigerated carriers. They hire and train new drivers to the highest road safety standards. They conduct audits and help flatbed carriers have fewer incidents. Plus, they monitor driver behaviour and offer re-training as required.
While conducting all of these tasks, Rangan expects his staff to keep their own occupational health and safety top of mind.
“I’m a really strong believer that if my staff feels they are working in a really safe and secure environment, productivity obviously increases. The worst-case scenario is if a (worker) slips and falls, it’s not only him in the hospital, but his entire family has a negative effect because now there’s no income coming in,” Rangan says. “It has a chain reaction on their lifestyle.”
Unfortunately, not all small businesses place such an emphasis on OHS. In fact, many research papers have found that workplace injury and fatality rates tend to be higher in small businesses than large ones. With 1.12 million Canadian workplaces employing fewer than 50 employees, health and safety needs to be actively promoted among small businesses — especially since they make up 95 per cent of Canadian employers.
Industries that are dominated by small businesses — such as construction, manufacturing and agriculture — tend to include a lot of high-risk activities, which may be one explanation for the higher rates, says Kim Cullen, an assistant professor at Memorial University of Newfoundland in St. John’s.
Another explanation is that small businesses may be unaware of the specific OHS laws and regulations they are expected to follow — or they are just not well-educated on the hazards their workers face.
“With any one small business, there are very seldom accidents that take place. It’s a pretty rare occurrence within any one workplace,” says Cullen. “That’s sometimes why there’s a disconnect between small places recognizing that there is this higher risk. They don’t see it, so it’s a sense they don’t necessarily have.”
The concept of health and safety can be quite overwhelming for small business owners, and they often don’t even know where to start, says Judy Kainz, director of prevention services at the Workers’ Safety and Compensation Commission (WSCC) of the Northwest Territories and Nunavut.
“They have this perception of a 6-inch binder sitting on their shelf,” she says.
One way to reduce the anxiety is for the business owner to not take it all on themselves, especially since legislation and regulations are constantly changing.
“Get your whole group involved; delegate it,” says Kainz. “It doesn’t have to be solely the employer’s responsibility to build the book — it’s everybody’s.”
When Rangan hired Harshad Solanki, he quickly tapped into Solanki’s strong health and safety background — he worked as a safety officer in India for over five years.
“Before Harshad came on board, I was just like the other owners, I have to say that. I had 10 to 12 staff; this was definitely not a priority. But when Harshad came on board, I saw his passion for it and I said, ‘Why don’t we implement something for our own staff as well?’” Rangan recalls. “He has been instrumental in putting all the safety policies in place and guiding us through this process.”
If they can’t hire any safety help, owners might be able to find a manager, supervisor or worker who can be a safety advocate.
“It’s really important to foster that and find someone who has that passion in your organization… That makes your life so much easier,” says Kainz.
Cost is an often-cited barrier to occupational health and safety for small businesses, which is understandable, given the many demands they face, including trying to stay fiscally viable, says Cullen. According to The Impact of Regulatory Costs on Small Firms from the United States’ Small Business Administration Office of Advocacy in 2010, businesses with fewer than 20 employees pay about US$250 more per employee for OHS and homeland security regulations than firms with 500 or more employees.
From Rangan’s perspective, having a health and safety program in place is a much cheaper alternative than not having one.
“If there is no safety in place, there is going to be a cost to it one way or another. You are saving money initially by not putting money into safety, but in the long run, you’re taking a risk,” he says. “By not having a safety program, you’re not having a calculated risk, you’re just winging it — and that’s the most dangerous thing that anybody can do.”
When trying to get buy-in for safety from his clients, Rangan uses the example of how much a motor vehicle collision costs: the truck is down, a deductible has to be paid, insurance rates go up, the driver is out of work, the cargo might be damaged and the company might lose that client.
“A safety program for you per month is going to cost you $5,000. Now, all these (accident-related) costs will be roughly $70,000. How many loads do you have to do to recover this money?” he asks.
Additionally, a safety program can reduce turnover and sick days, improve productivity and retain employees, says Cullen.
One way to alleviate the costs associated with health and safety for small businesses is to reach out to vendors and suppliers. Many safety suppliers offer free framework documents and product samples, and they often have a wealth of OHS information that they are keen to share with their loyal customers.
Rangan is part of Ontario’s Infrastructure Health and Safety Association and various trucking associations, and he regularly draws on the networking opportunities and resources available. These organizations also have regular safety meetings for members, which he attends.
“People bring up different issues and we end up learning about the industry, about safety and health,” he says.
Going in on costs with other small businesses is another way to save money. This is a tactic used in the Northwest Territories where the price tag on OHS training can be steep. A $250 course offered in Edmonton can run a few thousand up North, after a trainer is flown in and their accommodations paid, Kainz says.
Another barrier small businesses face is that health and safety legislation is often designed with large, unionized companies in mind.
To navigate this barrier, small businesses may need a bit more guidance than others. WSCC’s Occupational Health and Safety Program Guide for Small Businesses gets down to the basics of what these companies really need — and it’s not a “great, big program,” says Kainz. The agency offers workshops for small businesses where they walk away with a completed health and safety policy.
“They need somebody to hold their hand while they write it — ‘You’re here for the day, let’s get this done,’” says Kainz. “It’s putting it in baby steps.”
In addition to information tailored to company size, information targeted to different industries can be beneficial, says Cullen.
“Certain industries have different types of occupational health and safety risk factors, so targeting the information that they are receiving to their sectors is helpful for them to see, ‘How does it relate to the work I’m doing on a day-to-day basis?’” says Cullen. “They need that information presented to them in an easy to access way.”
Kainz stresses the importance of owners not being afraid to ask questions — before it’s too late.
“For me, as the regulator, I would far sooner you pick up the phone and call me and say, ‘I got this job, this is what I am thinking. Does this make sense? Is it in compliance?’” she says. “I would far sooner say, ‘You have to look at this section of the legislation’ or ‘You need to go talk to this group,’ than I would them calling me and saying, ‘We’ve had a tragedy.’”
When developing legislation or new regulations, governments should consult with small businesses. Oftentimes, policies don’t fit the reality of the small-business workplace, says Cullen, so it’s important to bring these employers in on the ground floor to contribute to the discussion.
Yet another barrier that small businesses face is they can have a tendency to see risk as an individual issue. One reason for this may be that workers are given a lot of autonomy and responsibility over their work, explains Cullen. For example, construction workers are often members of trade associations, follow their own rules and care for their own equipment. This can result in a disconnect between a worker’s autonomy and the employer’s overall responsibility for safety.
“There is this expectation or onus that’s unfair, perhaps, but I have seen it myself,” she says. “I have a number of small business owners who, when I get into conversations with them, they tell me, ‘Well so-and-so fell down the stairs. That’s his job; he needs to know how to walk down stairs.’ But were there safety rails? What was the nature of the work? Were there obstructions in the way?”
According to Safety Activities in Small Businesses by the National Institute for Occupational Safety and Health (NIOSH) in Washington, D.C., small business managers are likely to see workplace incidents as due to factors outside their control, and they regularly underestimate the dangerousness of their work activities. In Improving Health and Safety in Small Businesses by the Institute for Work and Health (IWH) in Toronto, researchers found that small businesses downplay risks and both owners and workers see hazards as part of the job.
At Vagans, Rangan takes full responsibility for safety and he is held accountable by his open-door policy.
“We want to keep our staff’s eyes and ears open to find out if there is something we can do better or if something’s wrong,” he says. “Staff are not afraid to talk about it.”
The company holds monthly safety meetings where staff are encouraged to participate and give their input. As the company began to grow, one suggestion was for benefits plans, which is currently in the works. Rangan is making sure the packages cover not just basic medical and dental, but also psychological services, including an employee assistance program. He repeatedly emphasizes the importance of supporting workers’ mental health because it benefits both the employees and the business.
Just like developing a business plan, owners should take the time to develop a safety plan as part of their start-up process, Kainz recommends. They also need to lead by example and understand that the risk belongs ultimately to them.
“Yes, workers take risks, but is it because they have been led to believe it’s acceptable to do so? You know, ‘My employer doesn’t wear a seat belt when he is driving the company vehicle, so why should I?’” Kainz says.
Regularly communicating to employees about health and safety is a crucial component in any successful health and safety management program. In fact, it was a common thread among all three winners of Ontario’s Workplace Safety and Insurance Board (WSIB)’s Small Business Health and Safety Leadership Awards in 2018. Monday morning safety talks, information inserted into paycheques and safety boards in all facilities are just some ways the winners communicate important safety messages to their staff.
Small businesses need to pay particular attention to occupational health and safety because all it takes is one incident to put them out of business, Kainz says. It affects their reputation; clients will become hesitant to hire them and other companies reluctant to work with them. Especially in the age of social media, all it takes is one picture on Facebook of a worker at heights without fall protection to do lasting damage.
“At the end of the day, it’s their name that’s going to be splashed on the newspaper and in court,” Kainz says. “It’s their pocketbook. They have much to lose.”
If a small business does sustain a workplace incident, it can have serious consequences on the social dynamics within the company. Many small businesses are made up of family and friends — or they quickly become so — and an incident can be hard on everyone.
“I have seen too often where there is a serious incident or fatality and they are paralyzed because that was their brother, that was their friend as much as it was an employee,” says Kainz.
Small business owners are often close with their employees’ children and families, so when something bad happens, they really feel it, she adds.
Rangan shudders at the thought of one of his workers getting hurt. For him, putting a health and safety program in place is of the utmost importance because he knows that he is doing everything he can to protect his employees.
“I have a moral responsibly for my staff,” he says. “If something goes wrong, I have to live with that, and if I tried to cut short on something and that costed us, that’s really hard for me to live with.”
Developing an OHS Program
Often small business owners address safety issues verbally. To show due diligence, you have to document your safety program. If you’re an owner, this checklist can help you put an OHS program in place.
1. Do you have an OHS policy?
Make sure to have a written policy statement.
2. Do you, your supervisors and workers know and understand their OHS responsibilities?
OHS roles and responsibilities should be outlined within the policy statement.
3. Have you identified hazards?
Make a comprehensive list of hazards in your workplace.
4. Do you have your hazard controls in place?
Conduct regular job hazard analyses; implement job-specific safe work procedures; have a risk assessment rating for identified hazards.
5. Do your workers have the training and supervision to perform their jobs safely?
Provide a new worker orientation checklist and have readily available worker training records, such as for WHMIS and supervisor safety training.
6. Do you regularly discuss OHS issues with your workers?
Safety talks should be written and compiled in a safety talk log book.
7. Do you regularly check, service, and maintain all workplace equipment, machinery and tools?
Maintenance checklists, pre-shift inspection checklists and procedure checklists should be posted.
8. Do you have the following items?
• Emergency procedures posted at the work site
• First-aid kits
• First-aid log book to track injuries and ensure kit is replenished
• An injury reporting procedure
• Injury report form.
9. Do you have investigation procedures in place?
Along with a policy and procedure, there must be an investigation report form.
10. Do you maintain records and review your program?
Inspection reports and review logs are important documents to have on hand.
Source: Occupational Health and Safety Program Guide for Small Businesses, Workers’ Safety and Compensation Commission (WSCC) of the Northwest Territories and Nunavut
This article originally appeared in the June/July 2019 issue of COS.