How the industry has moved from 'missing fingers' and archaic attitudes to mental health
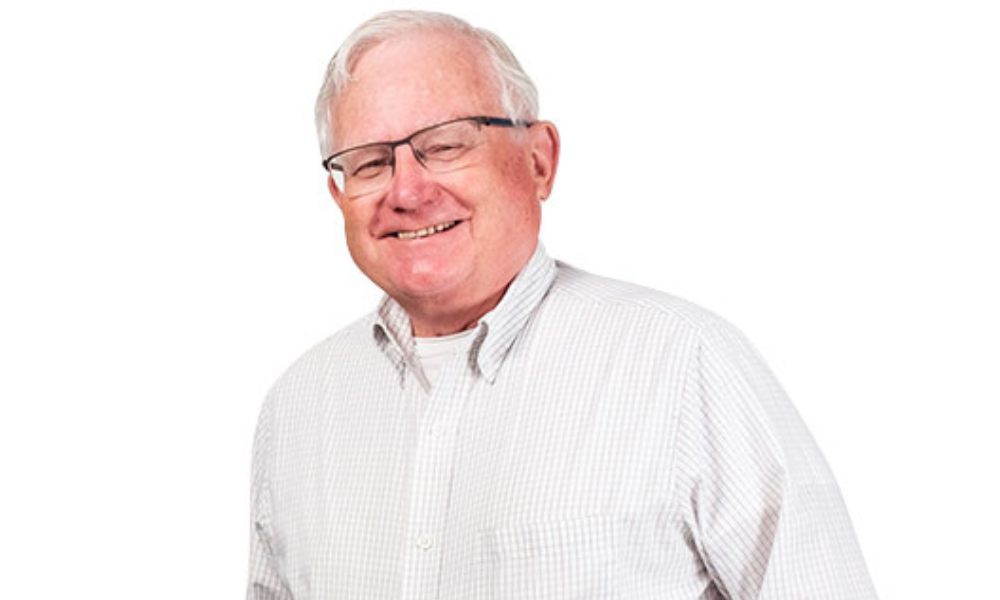
Canadian Occupational Safety is celebrating 60 years of publication in 2023. To mark the occasion, we are writing a series of articles that look back on the industries we cover to explore how safety practices have changed over the years.
Canadian manufacturing has come a long way since the 1970s, and Neal Curry has witnessed the transformation of an industry that wasn’t concerned if people lost limbs on the job, to one that cares deeply about the safety of its workers, both their physical wellbeing, and more frequently their mental health as well.
“I started working full time after graduating college in Ontario in a punching plant, and it was very different back then, almost everybody was missing some fingers,” laughs Curry. Fast forward about 50 years later, Curry is now the executive director of Made Safe, an initiative of the Canadian Manufacturers & Exporters.
Made Safe is based in Manitoba and provides training, certifications, and consulting to the manufacturing industry. Curry knows where the industry came from, where it is, and where it is going.
Painful past
Curry describes a tough atmosphere when he first started his career. “The only reason to miss work was a death in the family, preferably your own. A little bit of dark humor, but that was the kind of attitude,” he chuckles.
Curry was working in a furniture operation in the 1970s when a new law was passed that doubled WCB premiums for employers that had accidents rates higher than a certain threshold. “The company I was with had that imposed on them. And me as a young rookie industrial engineer, they sent me off to a government course to learn about safety.”
He says the training was “pretty rudimentary,” but it pushed the idea that the employer is responsible for the safety of its employees, which was somewhat novel at the time. Those values matured, the laws shifted in favour of workers’ rights, and the fines for non-compliance steadily increased.
“It just gradually evolved,” says Curry, “and of course, it starts with the big companies first because they have the most exposure.” Then the smaller organizations follow, but they often can’t keep up, and Curry says in some cases, “the fight is still going on.”
Current challenges
One area where challenges persist is within metal manufacturing and the welding trade. The process can release harmful toxins and the exposure limits are strict according to Curry.
He says larger companies can hire industrial hygienists and control the hazards, “but some of the smaller ones that maybe started off with one welder and then progressed to several welders, they see this as a huge problem to overcome… manganese exposure is one of the main issues that we're facing today.”
Point of use or source capture is a control method that involves sucking the fumes away while the welder has a face shield, with fresh air on the inside. “Those solutions are expensive,” explains Curry, and in addition to getting buy-in from employers, Curry says the worker’s themselves need to be convinced that while the PPE may be uncomfortable, it’s for their own good, “especially if you've been doing it a certain way for years and you haven't seen the bad effects yet.”
Staying up to date on training and best practices can also be met with pushback. “The safety management system training course is three days,” Curry will explain to an employer, and the response is “I can’t take somebody off for three days.” Curry says some employers want safety management systems to come in a box they can place on their shelves, “but it doesn't work that way.”
Another area where we see a lot of fines still being issued is around guarding. Curry says pinch points have always been one of the main hazards in manufacturing, and the exact hazard is always changing, because the advancement of technology is rapid.
“It's very difficult to guard a machine for all the different configurations you might want to make on that machine,” explains Curry, “and so that is an issue for sure.”
He suggests employers work closely with suppliers and make sure they commit to guarding the machine to the CSA guarding standards.
“Don't go out and buy an unguarded machine and then think you're going to guard it afterwards because it will probably cost you more than if you had it done right in the first place.”
Where the industry is going
Manufacturing is heading down a path many other industries are also in the early stages of exploring. Born from a past where little sentiment was given for physical wellbeing, “mental health is now becoming a huge issue,” says Curry.
He believes mental health is where ergonomics was 20 years ago. “People are very aware that how you design your workstations has a major impact on ergonomic health, which is the biggest single cause of accidents in most jurisdictions…I see mental health being the next wave of that.”
Physical harm can also lead to mental injuries. Curry says hurt workers have suffered trauma and can experience symptoms of PTSD. “That's a big challenge for people who have return-to-work policies on how to manage that properly.”
Curry says whether it’s physical harm or mental pain, these are problems that will keep people from entering the manufacturing industry, which is one of the biggest challenges of all. “We all know that there is a problem attracting employees these days,” says Curry.
“If you can say we've got an excellent safety program, we don't hurt our people, that has to help with your recruitment situations.”
Canada needs workers to make products. Employers need to protect those workers.