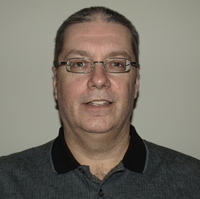
When workplace accidents or incidents occur, employers perform investigations to determine the root causes and to prevent these events from happening again. They want to determine if, within their safety managed system, all issues with the potential to cause accidents or incidents have been properly addressed.
I believe many employers overlook a very important factor in their investigations: “situational awareness”.
The concept of situational awareness is certainly not a new one. It has been recognized by military organizations for many years, especially in the air force. Its application has expanded over time to include other fields of work, such as civil aviation and nuclear power plants, which require complex decision making processes to help them mitigate any serious consequences created by their operation.
Dr. Mica Endsley's widely accepted definition of ‘situational awareness’ states that it is “the perception of elements in the environment within a volume of time and space, the comprehension of their meaning, and the projection of their status in the near future.”
The situational awareness model requires that a person, or a group of people, assess and become aware of relevant factors in their current environment, consider any implications of these factors and foresee future consequences.
Obviously, situational awareness can be widely-applied, even on work sites, to help workers function properly within their specific work environment.
From a health and safety perspective, situational awareness means being aware of the surrounding conditions in your immediate work area and recognizing and dealing with unsafe work conditions before they become an issue. It can probably be more accurately described as a hazardous work condition assessment.
In addition to identifying job hazards, based on the last time the work was performed, situational awareness requires conducting a visual assessment of the actual working conditions in the workplace before the new work begins. This is to identify any potential deviations from approved workplace standards.
Looking back on past incident or accident investigations will most likely confirm that events could have been prevented or hazards could have been identified, prior to working in the area, had the work plan included situational awareness.
Examples of a lack of situational awareness would be undetected ice hanging dangerously from a building, poorly secured material on a roof becomes airborne during a wind storm, or tools that were left in a position where they could easily fall if disturbed.
Job safety planning
The job safety planning process has often taken into account data from studies involving accident and incident theory. Typical results from accident ratio studies are not meant to predict the future escalation of these events. They should be seen as an indication that your safety managed system needs improvements to increase the prevention of incidents and accidents.
Many of the job safety plans I’ve reviewed over the years primarily relied on past experiences of the way a job had last been performed in the workplace.
The job safety planning process is designed to help workers identify and control workplace hazards, including the risk of dangerous contact with an energy source.
Energy barrier analysis
According to the concept of an energy barrier analysis, if we fail to eliminate a dangerous energy source, it becomes an unwanted energy. If we fail to control the unwanted energy, it becomes a hazard and if we fail to protect the worker from the hazard, it can lead to a potential injury.
Incident or accident investigations regarding unwanted energy demonstrate that the job safety planning process often tends to be typically focused on the task at hand while ignoring other potentially unsafe conditions in the workplace. Written and verbal job safety planning must incorporate the need to respond to any changes encountered during the work.
Unsafe working conditions
Workplace conditions are usually not static and they can change significantly at any time. Therefore, they need to be continuously monitored. This includes before, during and after completion of the job.
The image shown below is an Unsafe Working Condition Awareness diagram.
Again, we see an accident/incident theory pyramid, but in the shaded section below it, we see that certain circumstances, such as deviations from standards and practices, can lead to incidents and accidents.
No energy transfer or exposure to the worker has occurred at this point and an unsafe practice has not yet become a factor.
This is specifically the area where we need to concentrate our efforts when implementing a job safety plan. You can avoid escalating up the pyramid and having unnecessary incidents or injuries if unsafe working conditions, unsafe work practices and workplace hazards are addressed before they become an issue.
Examples of unsafe conditions are unguarded equipment, poor housekeeping, insufficient barriers, defective tools, poor maintenance and environmental issues (dust, light, noise, etc.).
Examples of unsafe work practices are: using untrained workers, using workers that are not authorized to operate the equipment, improperly using tools or equipment, bypassing barriers and not using personal protective equipment.
The best people to identify and initiate a response to unsafe conditions in the workplace are the workers. They are the ones who perform the work on a regular basis and are knowledgeable and trained to operate equipment and tools. If the safety concern is beyond their control, they can report the issue to their immediate supervisor for a response.
At morning tailboard meetings, the supervisor should review the job safety plan with the workers and identify specific issues that may impact the workplace location.
The supervisor can also perform job site visits to review the work site and ensure that issues, which were not identified in the original safe work plan, are addressed. Depending on the issue, this could involve stopping the job, re-assessing and re-planning the work.
Having a functioning internal responsibility system within your organization will greatly enhance cooperative interaction between worker and supervisor in addressing issues.
In my assessments of incident or accident investigations, most of the unsafe working conditions were linked to the environment element of the safety managed system. This is also consistent with the definition of situational awareness. I believe this is due to the fact that the environment can be more difficult to control as compared to the other elements of the safety managed system. People, procedures and hardware can be more easily managed by the line organization.
In considering the environment element of a safety managed system, bear in mind that it encompasses more than just outdoor issues:
Weather conditions
• high winds, lightning, heat/cold, rain/snow
Lighting conditions
• adequate intensity (indoors), time of day (outdoors), visibility
Air quality conditions
• dust/particulate, gases, temperature/humidity, O2 deficiency
Physical work conditions
• housekeeping, uneven surfaces, soil conditions, unsecured tools/equipment, heights
So, what is the best way to address situational awareness at work?
Remember that the workplace environment is where you’ll need to focus most of your attention to address situational awareness issues. You’ll need to maintain safety standards on your site to help prevent the creation of unsafe conditions and unsafe practices which can lead to incidents/accidents.
This can be accomplished by ensuring that your organization is complying with legislation, that they have an inspection process for tools/equipment, that they support supervisory leadership, that they maintain good communications, that they have a process for workplace observations, and that they follow their procedures.
Complying with legislation
• ensure that workers understand and comply with the OH&S Act / Regulations
• workers use or wear the personal protective equipment required by the employer
• report any contraventions or the existence of any hazard
• take every precaution reasonable under the circumstances for the protection of the worker
Inspection process
• ensure workers are using the right tool for the job
• ensure tools and equipment are inspected for defects prior to use
• do not modify tools or equipment
• remove defective tools or equipment from service
Supervisory leadership
• ensure that supervisors receive appropriate training
• ensure that they conduct daily tailboards
• that they perform daily work site visits
• that they address issues collectively with workers (IRS)
Communication
• use the three-way communication process
• workers immediately report any issues or hazards to their supervisor
• workers take advantage of tailboard and safety meetings to discuss issues
• managers review relevant safety information with staff
Workplace observation process
• keep the work area clean (housekeeping)
• inspect the job site for potential issues prior to starting the work
• secure tools and equipment from falling
• be aware of other work groups in the area
Procedures
• ensure that workers have access to relevant procedures on site
• workers must follow the lock-out/tag-out process
• review the H&S managed system for the organization (such as OHSAS 18001)
• manager keep the information relevant by updating the procedures on a regular basis
It is very easy to become complacent about unsafe conditions in the workplace since most of these conditions do not necessarily become an issue. However, the possibility that a dangerous situation can occur is too serious for an organization to ignore. Prevention that includes situational awareness is a much more comprehensive approach to safety.
--------------------------
Guy Chenard, CRSP, C.E.T., is a safety professional with Ontario Power Generation.
I believe many employers overlook a very important factor in their investigations: “situational awareness”.
The concept of situational awareness is certainly not a new one. It has been recognized by military organizations for many years, especially in the air force. Its application has expanded over time to include other fields of work, such as civil aviation and nuclear power plants, which require complex decision making processes to help them mitigate any serious consequences created by their operation.
Dr. Mica Endsley's widely accepted definition of ‘situational awareness’ states that it is “the perception of elements in the environment within a volume of time and space, the comprehension of their meaning, and the projection of their status in the near future.”
The situational awareness model requires that a person, or a group of people, assess and become aware of relevant factors in their current environment, consider any implications of these factors and foresee future consequences.
Obviously, situational awareness can be widely-applied, even on work sites, to help workers function properly within their specific work environment.
From a health and safety perspective, situational awareness means being aware of the surrounding conditions in your immediate work area and recognizing and dealing with unsafe work conditions before they become an issue. It can probably be more accurately described as a hazardous work condition assessment.
In addition to identifying job hazards, based on the last time the work was performed, situational awareness requires conducting a visual assessment of the actual working conditions in the workplace before the new work begins. This is to identify any potential deviations from approved workplace standards.
Looking back on past incident or accident investigations will most likely confirm that events could have been prevented or hazards could have been identified, prior to working in the area, had the work plan included situational awareness.
Examples of a lack of situational awareness would be undetected ice hanging dangerously from a building, poorly secured material on a roof becomes airborne during a wind storm, or tools that were left in a position where they could easily fall if disturbed.
Job safety planning
The job safety planning process has often taken into account data from studies involving accident and incident theory. Typical results from accident ratio studies are not meant to predict the future escalation of these events. They should be seen as an indication that your safety managed system needs improvements to increase the prevention of incidents and accidents.
Many of the job safety plans I’ve reviewed over the years primarily relied on past experiences of the way a job had last been performed in the workplace.
The job safety planning process is designed to help workers identify and control workplace hazards, including the risk of dangerous contact with an energy source.
Energy barrier analysis
According to the concept of an energy barrier analysis, if we fail to eliminate a dangerous energy source, it becomes an unwanted energy. If we fail to control the unwanted energy, it becomes a hazard and if we fail to protect the worker from the hazard, it can lead to a potential injury.
Incident or accident investigations regarding unwanted energy demonstrate that the job safety planning process often tends to be typically focused on the task at hand while ignoring other potentially unsafe conditions in the workplace. Written and verbal job safety planning must incorporate the need to respond to any changes encountered during the work.
Unsafe working conditions
Workplace conditions are usually not static and they can change significantly at any time. Therefore, they need to be continuously monitored. This includes before, during and after completion of the job.
The image shown below is an Unsafe Working Condition Awareness diagram.
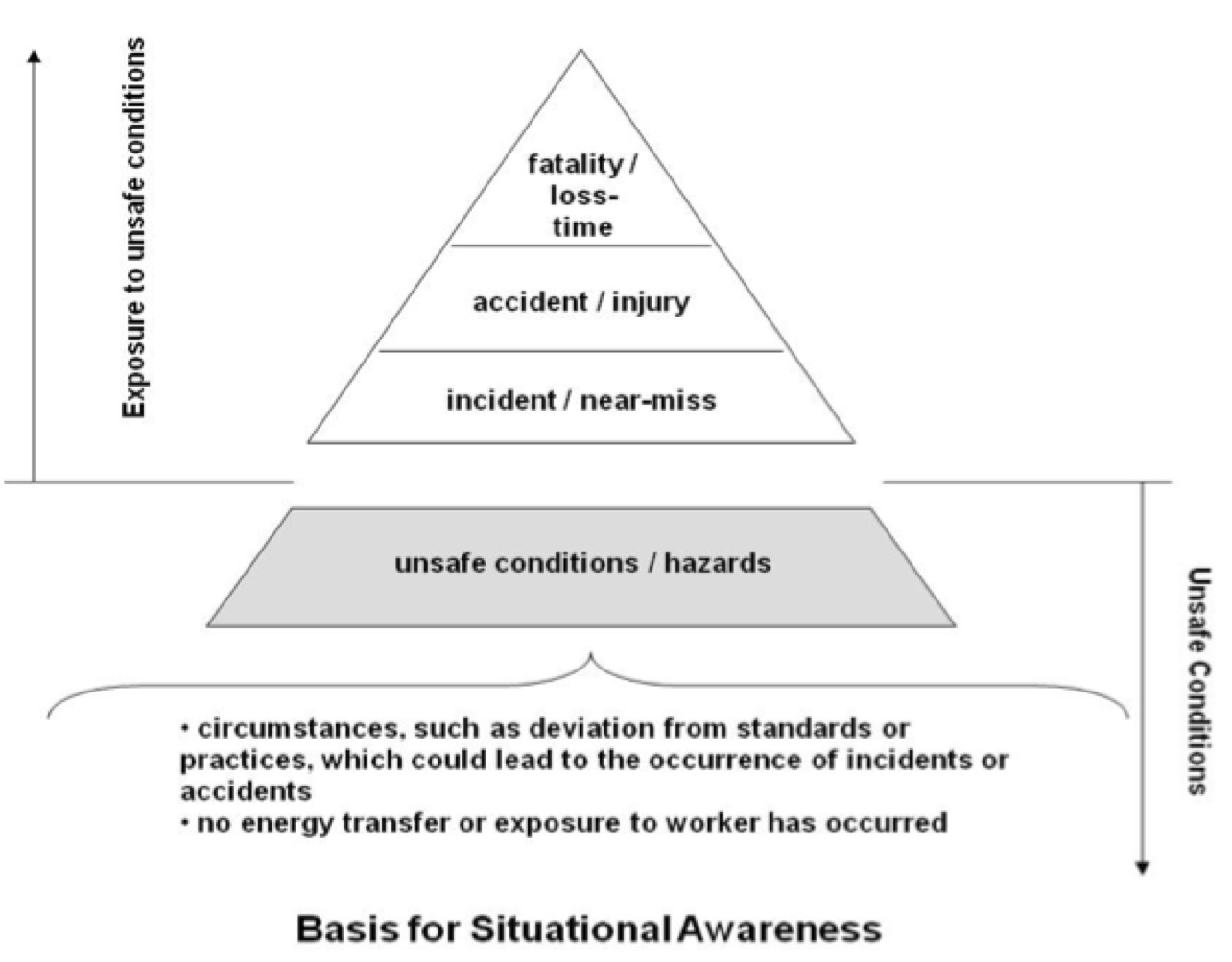
Again, we see an accident/incident theory pyramid, but in the shaded section below it, we see that certain circumstances, such as deviations from standards and practices, can lead to incidents and accidents.
No energy transfer or exposure to the worker has occurred at this point and an unsafe practice has not yet become a factor.
This is specifically the area where we need to concentrate our efforts when implementing a job safety plan. You can avoid escalating up the pyramid and having unnecessary incidents or injuries if unsafe working conditions, unsafe work practices and workplace hazards are addressed before they become an issue.
Examples of unsafe conditions are unguarded equipment, poor housekeeping, insufficient barriers, defective tools, poor maintenance and environmental issues (dust, light, noise, etc.).
Examples of unsafe work practices are: using untrained workers, using workers that are not authorized to operate the equipment, improperly using tools or equipment, bypassing barriers and not using personal protective equipment.
The best people to identify and initiate a response to unsafe conditions in the workplace are the workers. They are the ones who perform the work on a regular basis and are knowledgeable and trained to operate equipment and tools. If the safety concern is beyond their control, they can report the issue to their immediate supervisor for a response.
At morning tailboard meetings, the supervisor should review the job safety plan with the workers and identify specific issues that may impact the workplace location.
The supervisor can also perform job site visits to review the work site and ensure that issues, which were not identified in the original safe work plan, are addressed. Depending on the issue, this could involve stopping the job, re-assessing and re-planning the work.
Having a functioning internal responsibility system within your organization will greatly enhance cooperative interaction between worker and supervisor in addressing issues.
In my assessments of incident or accident investigations, most of the unsafe working conditions were linked to the environment element of the safety managed system. This is also consistent with the definition of situational awareness. I believe this is due to the fact that the environment can be more difficult to control as compared to the other elements of the safety managed system. People, procedures and hardware can be more easily managed by the line organization.
In considering the environment element of a safety managed system, bear in mind that it encompasses more than just outdoor issues:
Weather conditions
• high winds, lightning, heat/cold, rain/snow
Lighting conditions
• adequate intensity (indoors), time of day (outdoors), visibility
Air quality conditions
• dust/particulate, gases, temperature/humidity, O2 deficiency
Physical work conditions
• housekeeping, uneven surfaces, soil conditions, unsecured tools/equipment, heights
So, what is the best way to address situational awareness at work?
Remember that the workplace environment is where you’ll need to focus most of your attention to address situational awareness issues. You’ll need to maintain safety standards on your site to help prevent the creation of unsafe conditions and unsafe practices which can lead to incidents/accidents.
This can be accomplished by ensuring that your organization is complying with legislation, that they have an inspection process for tools/equipment, that they support supervisory leadership, that they maintain good communications, that they have a process for workplace observations, and that they follow their procedures.
Complying with legislation
• ensure that workers understand and comply with the OH&S Act / Regulations
• workers use or wear the personal protective equipment required by the employer
• report any contraventions or the existence of any hazard
• take every precaution reasonable under the circumstances for the protection of the worker
Inspection process
• ensure workers are using the right tool for the job
• ensure tools and equipment are inspected for defects prior to use
• do not modify tools or equipment
• remove defective tools or equipment from service
Supervisory leadership
• ensure that supervisors receive appropriate training
• ensure that they conduct daily tailboards
• that they perform daily work site visits
• that they address issues collectively with workers (IRS)
Communication
• use the three-way communication process
• workers immediately report any issues or hazards to their supervisor
• workers take advantage of tailboard and safety meetings to discuss issues
• managers review relevant safety information with staff
Workplace observation process
• keep the work area clean (housekeeping)
• inspect the job site for potential issues prior to starting the work
• secure tools and equipment from falling
• be aware of other work groups in the area
Procedures
• ensure that workers have access to relevant procedures on site
• workers must follow the lock-out/tag-out process
• review the H&S managed system for the organization (such as OHSAS 18001)
• manager keep the information relevant by updating the procedures on a regular basis
It is very easy to become complacent about unsafe conditions in the workplace since most of these conditions do not necessarily become an issue. However, the possibility that a dangerous situation can occur is too serious for an organization to ignore. Prevention that includes situational awareness is a much more comprehensive approach to safety.
--------------------------
Guy Chenard, CRSP, C.E.T., is a safety professional with Ontario Power Generation.