BASF safety head shares 'biggest challenge' and what led to 'best year ever'
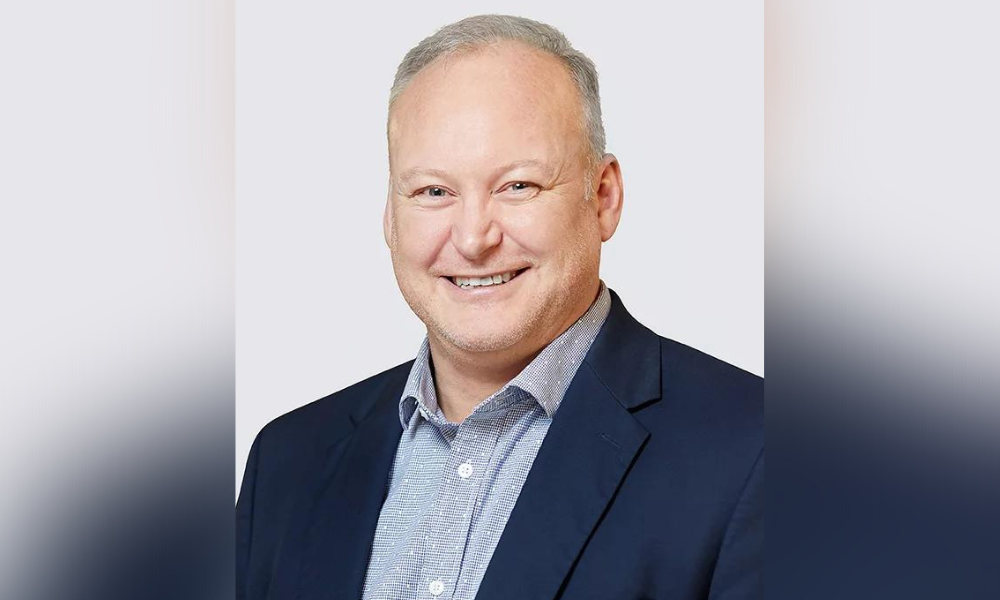
“This is by far our best year ever,” says Sean Cammaert proudly. He is the head of safety for BASF Canada, and he has been working hard over the past eight years to change the behaviour of employees at the chemical company.
Cammaert says there have only been two time-lost injuries in 2022 at the company that employs 1,200 -1,500 people depending on the time of year. Neither of those injuries were severe. It is the safest year on record, and he attributes it to a cultural change that’s been taking place for the better part of the last decade.
“The focus used to be very fear, top-down driven. You will do this because this is the rule. If you don't do it, you're going to lose your job,” explains Cammaert as he describes the safety atmosphere he grew up in during the 1980s and 1990s while doing a “whirlwind tour in manufacturing.” He says there is a greater emphasis now on changing behaviours to meet safety requirements as opposed to culture of enforcing rules, “and I think this way, is becoming much more impactful for people because we relate it back to their families.”
Getting personal and reminding workers that everyone at the company wants them to go home unharmed is the type of positive reinforcement becoming more commonly applied in workplaces. You might think at a company like BASF, the chemicals would be the main hazard to be concerned about, but Cammaert says that is not the case.
“Our biggest hazard, believe it or not, are forklifts,” says Cammaert, who recalled a severe near-miss earlier this year involving a transport truck pulling away from a loading dock while a forklift operator was still driving into it. Cammaert says the forklift operator stopped just in time but came close to driving off the dock, and that is just once incident that has Cammaert focused on improving behaviour among forklift operators.
“People tend to rush now,” explains Cammaert, who says speed and the motivation to move product out the door can cloud the company’s safety-first vision. “My job is to lend a hand, influence change, and change the mindset of our sites that production, while it pays the bills, is not king. Safety is our core value and that has to be at the forefront of everybody's mind at all times.”
Putting safety ahead of production can sometimes lead to pushback from managers in other departments. “Every day actually, literally dealing with two situations as we speak,” laughs Cammaert, as he reflects on another incident involving forklift operators and masking requirements in a unionized environment. Cammaert says managers, especially those coming into Canada from another country, often need training on best safety practices.
But how do you change the way someone thinks? Cammaert says this is among his biggest challenges and he tackles it by encouraging a culture of positive reinforcement that starts at the top and trickles down through middle management to the frontline workers. “A lot of statistics and a lot of behavioral science tells us that behaviors will change over time. But it takes time, it's not a light switch,” explains Cammaert.
He says that’s why the company has invested in training leaders and doing peer-to-peer observations focused on what people are doing right while providing feedback on the desired behaviour. When a worker is doing something risky, Cammaert says that’s an opportunity for a conversation, “now we talk about it, and then we get the solution from the individual versus telling them what they have to do.”
Part of that discussion is reminding the worker they have a family waiting for them at home.