Training, awareness of surroundings needed to avoid unnecessary risks
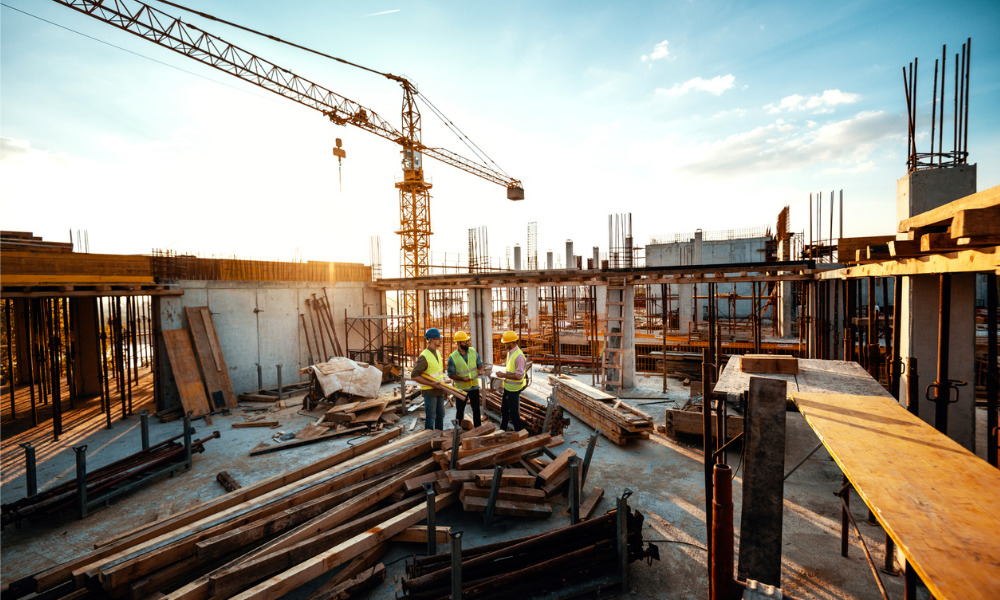
Most safety tips typically fall into the realm of common sense. But when a worker’s life is on the line, refreshers and reminders can never go amiss – especially in more hazardous sectors such as construction. Here are 10 effective safety tips that employers, workers and safety professionals need to be aware of on construction sites.
Keep a clean job site. There is no need to create unnecessary risks by having a job site covered in debris or junk, or with equipment that should have been packed away lying around. Keeping a clean job site will at least ensure that workers are not exposed to slips or trips, and that all necessary equipment is in the right place and ready to be used.
Be aware of your surroundings. Construction sites are frequently busy places, there’s a lot going on. Hazards can come from the ground (e.g. vehicle collisions, slips and trips over materials left lying around) and from the air (e.g. a heavy object falling from a platform). Workers and safety officers need to be aware of these hazards, and keep aware of their surroundings. Using safety signage can go a long way in raising awareness, and reminding workers of surrounding hazards during morning meetings can be very helpful.
Use fall protection. Working at heights is always a risky endeavour in any job, and especially on construction sites. Workers need to be using the correct fall protection equipment to ensure that they are not unnecessarily exposed to fall risks. Different equipment may be required depending on the situation. Safety professionals need to ensure that site safety is compliant with current regulations, and also confer with workers to see if there is anything else, or any additional equipment that can be used, to ensure optimal safety conditions.
Organize a risk management system. This should be practiced in every workplace, and especially in more hazardous settings such as construction sites. Risk management procedures inform how safety is effectively managed in a workplace. The system should be created once a risk assessment has taken place, and all necessary things are in place to ensure regulatory compliance. The risk management system should be communicated with workers so that everyone is on the same page.
Maintain communication. With workers all doing different tasks, safety officers and site managers need to make sure that they are in constant communication with all workers. Communication takes various forms, from equipment such as walkie talkies to ensure open lines of communication, to meetings and safety signage or accessible documentation to keep workers informed of all latest developments. Communication is key.
Implement new safety equipment. Safety is always evolving, with new risks popping up every so often. Safety folk may need to invest in new safety equipment to make sure that they are keeping up with these evolving risks. If new equipment is required, then workers should also be educated and trained on best practices when it comes to using this new equipment.
Use safety equipment. Following up from the previous point, this may seem like a very basic point to make, but workers should actually be using the safety equipment at their disposal. If not, they open themselves up to injuries and potentially even fatalities. If workers aren’t being encouraged or told to use the right equipment, that is a problem. If workers aren’t using the equipment, safety officers need to enquire as to why. Perhaps the equipment isn’t suited for the type of work being done, perhaps it is ill-fitting or outdated – ill-fitting equipment can create safety hazards (e.g. loose trousers can get caught in machinery).
Also ensure that necessary safety equipment (such as fire safety equipment) is clearly labelled and easily accessible.
Have clear procedures for using ladders. Ladders are a helpful bit of equipment, used to access higher elevations they can be linked to risks such as slips, trips or falls. This may seem very basic as most people know how to use a ladder, but clear safety protocols can always be helpful when using a ladder (e.g. how to properly set up a ladder, how to safely store it after use, etc.).
Ensure that everyone is aware of the safety regulations. Everyone on a construction site should at least have some awareness of necessary safety regulations. Safety professionals certainly need to be aware. Training goes a long way in making sure that this knowledge is understood and widespread. Even those who may have received initial training may get rusty, so a refresher course is always a good idea.
Stay out of busy work areas. Job sites are often busy areas, with each worker toiling away at their own tasks. Those who do not need to be on the site, and certainly in busy work areas, should simply not be hanging around there. Additional personnel may create unnecessary distractions, or get in the way of dangerous work, exposing the worker or the individual to risks. This should be clearly communicated with workers. If a worksite is overly busy, employers and safety folk may want to create designated rest or break areas (e.g. using industrial curtains or other safety screens) to remove individuals hanging around from busy work areas.