Company wins gold in chemistry category of Canada's Safest Employers awards
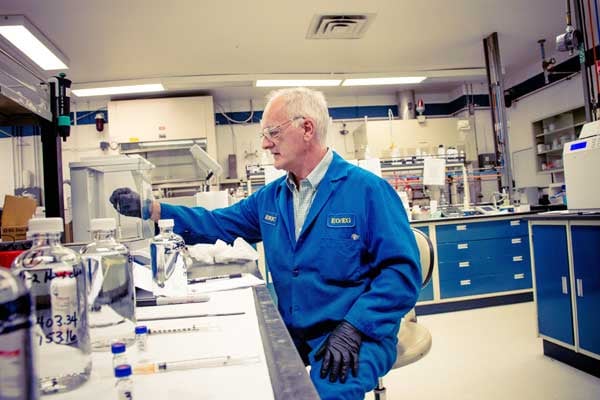
MEGlobal Canada doesn’t mind who sees its safety targets. The Alberta-based chemical company, which has manufacturing facilities in Fort Saskatchewan and Prentiss, has established a set of long-term sustainability goals, Focus 2020, aimed at maximizing environment, health and safety (EHS) performance. Targets include: 0.1 injury and illness rate; zero process safety events and zero transportation incidents. The targets are all listed on the company’s website.
“Few companies make these goals transparent and easily available for anyone to look at. In every category, we clearly said what we wanted to do,” says Pravind Ramdial, Responsible Care leader.
To minimize MEGlobal’s environmental footprint, the company aims to reduce greenhouse gas emissions by 30 per cent and chemical emissions by 50 per cent.
“We always set very aggressive goals,” says Rocco Schurink, vice-president of operations. “It’s part of our legacy to make sure that we are a respected member of our community and that tomorrow is better than today.”
External audits are conducted regularly at MEGlobal, Ramdial says. The Certificate of Recognition (COR) process allows auditors to identify gaps in the company’s safety management system and recommend improvements based on best practices in other industries.
Then there is a corporate external audit and insurance risk audits. Moreover, as a member of the Chemical Industry Association of Canada, MEGlobal also undergoes an audit every three years by the association to verify the company is meeting the ethics, principles and codes of the Responsible Care program, which promotes safe, responsible and sustainable chemical manufacturing.
“We feel our own auditing is good, but it’s better to ask others to have a look at how good you are,” Ramdial says.
In both the EHS and process safety systems, the safety team implements a second-level review for incidents, Schurink says. The review, which includes several managers, including himself and the safety and process safety managers, is called for all incidents, no matter how minor.
“For example, if we have a restart of a unit after a major turnaround, it is taken very seriously. Although I hold all production leaders responsible and accountable for the operation of his or her plant, none of them can re-start the plant without a peer review to make sure the plant is really ready to go,” he says.
At MEGlobal, which has 175 employees, process safety is considered just as important as personal safety. A manager dedicated to process safety has a network of contacts to ensure someone who’s responsible for the implementation of the process safety program is always in the plant.
Managers sit down with every new employee and discuss the company’s expectations, including those on safety. The new recruits are then required to send an email to Ramdial stating they understand the expectations and pledge their personal commitment to safety.
“We find that’s very personal and individuals can connect on that,” he says.
Managers regularly review incidents that occurred in other companies in the industry.
“We look at those as if they had happened in our own company, figure out where the gaps are and close them. It’s the only way to eliminate incidents: You learn from others,” Ramdial says.
Employees and contractors, who are all held to the same expectations, are required to step in and stop a job they consider unsafe.
“We’re very clear about our priorities, and nothing competes with safety,” Ramdial says. “Everyone knows this, and we continually emphasize it. Cost, schedule, whatever it may be, it will not affect our safety performance.”