How to implement a system to keep workers safe on job sites
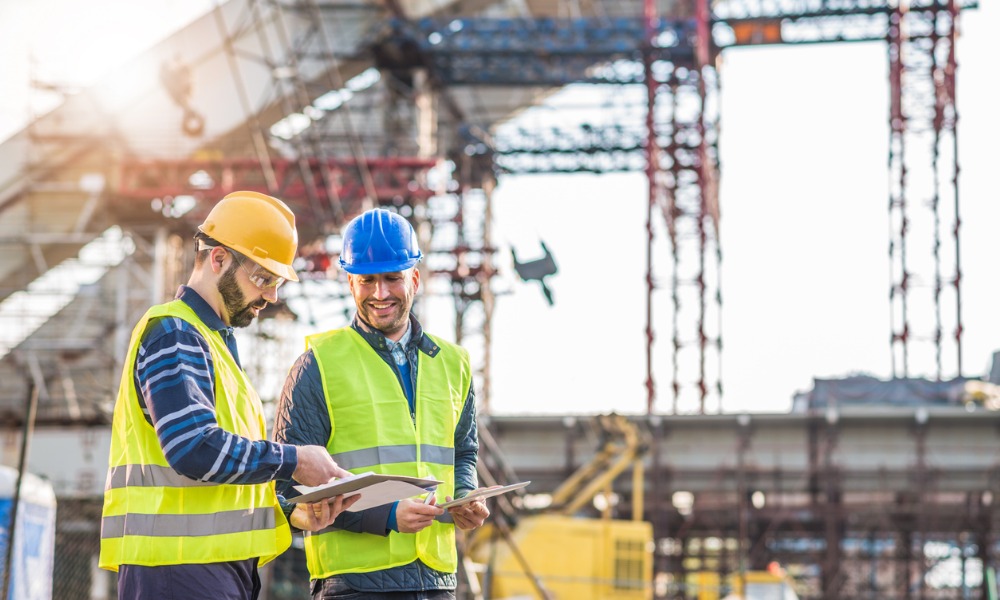
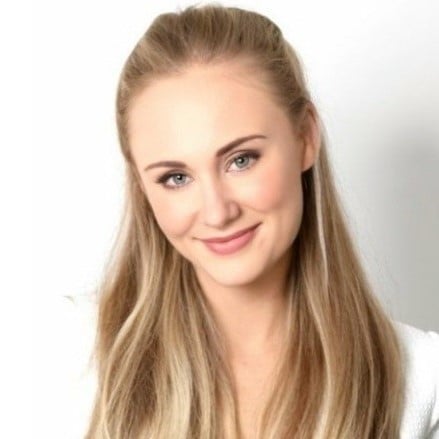
Installing or servicing electricity, water, heating and cooling systems, elevators, plumbing and boilers may involve hazardous conditions. You might face situations that endanger your safety and the safety of other building occupants.
An effective emergency safety protocol reduces the risks and ensures you know how to react in emergencies. Establish and rehearse emergency procedures for the highest level of safety at the job site.
Developing a safety protocol
A safety protocol reviews typical emergencies and establishes responses to keep you safe and comply with regulatory requirements. Here are the steps to develop one tailored to your situation.
1. Determine your risks
The risks you face when installing or servicing equipment may vary based on the type of work you perform. The Canadian Centre for Occupational Health and Safety shows that electrical contractors deal with injuries like electrocution, electric shock, burns and falls.
Other building equipment contractors face different concerns. Elevator installers are at risk of falling, electric shock and being struck by the elevator. In 2019, there were 14 injuries reported caused by elevator maintenance and installation hazards.
You must determine the risks for your industry to decide on the best safety protocols to implement.
2. Assess company safety resources
After determining the risks for a particular job, assess your safety resources, including personal protective equipment (PPE). You must select the proper type for the situation, keep it in good condition and ensure you use it when working on a job site. Your PPE should include:
- Hard hat
- Safety glasses
- Safety boots
- Hearing protection
- Respiratory protection
You may add or change equipment depending on the needs of a particular job.
Your safety resources may also include frequent equipment inspections for dangerous tools that could cause safety hazards if they don’t function properly.
3. Communicate about hazards
Safety extends to each worker and anyone on the job site during installation or maintenance. You must ensure people know the hazards and the proper safety gear to reduce risks. Communicate verbally with workers and use signs inside a building to indicate work in progress.
You must also establish emergency communication plans that indicate how you will notify everyone on your team. They should include the method of communication and the details of who notifies whom so everyone receives the proper warning.
4. Train your workers
An emergency safety protocol does the most good when everyone knows and understands their responsibilities in emergencies. Schedule regular safety training to keep everyone updated and give practical experience in handling emergencies.
Safety training ensures teams know how to respond and can do so efficiently during an emergency. Your training program should include education at the beginning of employment, when introducing new procedures, and annually to refresh skills and knowledge.
Implement a structured training program with hands-on learning opportunities to ingrain safety procedures into every team member.
Start planning emergency safety
Building equipment contractors face various hazards in the workplace, including falls, electrical shocks and other dangers. An emergency safety protocol ensures compliance with regulations, mitigates risks and improves project success.
Begin developing an emergency safety plan to stay safe on the job site.