Flammable liquids ignite easily and are used in almost every workplace. How can workers prevent these liquids from igniting and what to do if a fire occurs?
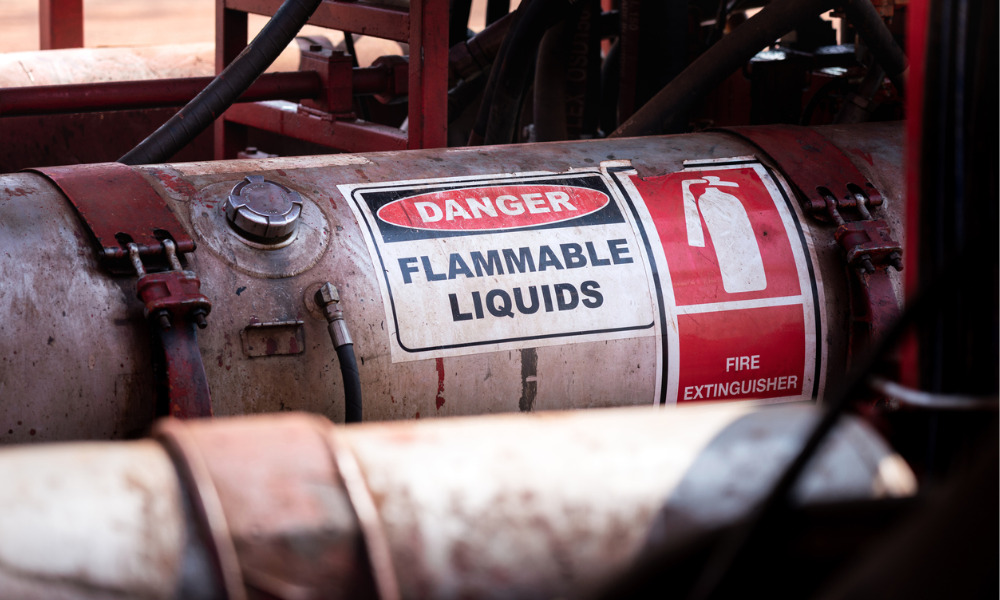
In July 2017, an Ottawa roofing company was installing a roof on a two-storey house. Three workers were on the home’s balcony when adhesive glue, a flammable liquid, caught fire. No fire extinguisher was available, and the workers had no way to escape from the balcony quickly. Two workers caught fire; the third suffered serious burns to the arms, legs and torso.
Flammable liquids produce vapours that can ignite or explode. They are used in a vast range of industries, and most workers will handle them at some time. It’s essential for managers and workers to know how to use these chemicals safely and reduce the chance of fire in their workplace.
Some of the most familiar flammable liquids include gasoline, paint thinners, cleaners, adhesives, paints, waxes and solvents. Their use is widespread in the automotive, oil and gas, food and pharmaceutical industries, as well as in laboratories and in manufacturing machine shops.
FLAMMABLE VERSUS COMBUSTIBLE LIQUIDS
Flammable liquids are distinguished from combustible liquids by their flashpoint, defined as the lowest temperature at which a flammable or combustible liquid gives off enough vapour to form an ignitable mixture with air. The flashpoints of flammable liquids are lower than those of combustible liquids.
Both types of liquid are classified according to their flashpoints and boiling points. Until recently, flammable liquids were considered to be those that had a flashpoint up to 37.8 C, while combustible liquids had a flashpoint at or above 37.8 C and below 93.3 C. The liquids were grouped into three classes, with all flammable liquids in Class 1, which was further divided into Classes 1-A, 1-B and 1-C. Combustible liquids were grouped into Classes 2 (flashpoints between 38 C and 60 C) and 3 (flashpoints between 60 C and 93 C).
However, in 2015, the Workplace Hazardous Materials Information System (WHMIS) modified its classification system for workplace chemicals to be more aligned with the Globally Harmonized System of Classification and Labelling Chemicals (GHS). According to WHMIS 2015, flammable liquids are those that catch fire at temperatures below or at 93 C.
Moreover, they are now classified into four categories. Flammable liquids that have a flashpoint below 23 C fall into categories 1 or 2, depending on their boiling point. Flammable liquids that have a flashpoint at or above 23 C fall into category 3 (flashpoint up to 60 C) or 4 (flashpoint from above 60 C but below or at 93 C).
The lower the number of the category, the more flammable the liquid is, says Anne-Marie Besliu, occupational health and safety specialist at Hamilton, Ont.-based Canadian Centre for Occupational Health and Safety (CCOHS). A mixture of flammable vapours and air ignites when the concentration of the vapours is within limits known as the lower flammability limit or lower explosive limit (LFL/LEL) and the upper flammability limit or upper explosive limit (UFL/UEL).
“If the vapour concentration in the air is less than the LFL/LEL, then the mixture is not flammable because it is too ‘lean’ to burn. If the concentration of flammable vapours is higher than the UFL/UEL, then the mixture will not ignite because it is too ‘rich’ to burn,” she says.
It’s important to check the safety data sheet (SDS) of each product handled in the workplace to check for the product’s upper and lower limits. This sheet provides key information on the chemical, including its hazards, safe use procedures, protective measures, proper personal protective equipment (PPE) and emergency procedures in case of a fire.
FIRE AND EXPLOSION HAZARD
For a flammable or combustible liquid to catch fire, three ingredients must be present, says Simon Fridlyand, president of Toronto-based S.A.F.E. Engineering. There must be a fuel (vapour); oxygen (air) and an ignition source. If the mixture of flammable vapour and air catches fire, the flames travel quickly through it.
A fire may occur when an ignition source is too close to the liquid’s surface, where there tends to be a high concentration of vapours. It can also occur when a worker is dealing with a high quantity of flammable liquid and the vapours are allowed to build up in the workplace atmosphere. If the concentration of vapours in air becomes hazardous, any ignition source can cause a fire.
When, in addition to the flammable mixture and ignition source, there’s also an enclosure — a storage tank or a room where flammable liquids are processed, for example — there could be an explosion. Explosions can be powerful, resulting in the collapse of an entire building.
PROPER HANDLING OF FLAMMABLE LIQUIDS
The handling and storing of flammable liquids requires knowledge of a variety of regulations, codes and standards, says Greg Hodgson, occupational hygienist in the department of Environment, Health and Safety at the University of Alberta in Edmonton. Employers must consult the fire code of the local jurisdiction and other applicable safety codes, as well as provincial occupational health and safety law.
“The OHS is usually specific to certain processes, where the fire code talks about general use, storage and such. I would check the fire code and then the OHS legislation for the specific requirements. It might go above and beyond the fire code,” he says.
When handling a flammable liquid, workers should aim to limit the vapour concentration in the air to prevent ignition. Before starting work, it’s important for them to be aware of the lower flammable and explosive limit and the upper flammable and explosive limit of the chemical they are handling. This will tell them the range of concentration within which the chemical is hazardous.
“Even when you’re working with small amounts of liquid, it’s evaporating, and the key is to control the vapour that’s coming off the liquid to prevent it from reaching the lower explosive and lower flammable limit,” Hodgson says.
At the same time, workers must eliminate or control ignition sources — open flames, hot surfaces, spark-producing mechanical equipment, electrical equipment, static electricity and welding and cutting operations — near the work area or in areas where vapours may accumulate. Flammable liquid vapours are heavier than air and tend to fall and gather in lower areas. If vapours are ignited in these spaces, the flame may travel back or “flash” back, to the flammable liquid.
The risk from some ignition sources, such as static electricity, can be very difficult to mitigate, Fridlyand says.
“Very low ignition energy is required to ignite flammable vapours; static electricity can be generated by your clothing. But also, as you work, when you transfer a flammable liquid from one container to another, the liquid generates static electricity on its own. Going through pipes, it generates static electricity by itself. That’s why there’s always a requirement for grounding and bonding,” he says.
While transferring flammable liquids from one container to another, he adds, the containers must be electrically bonded to each other or electrically grounded.
Sparks are generated by electrical equipment. There should never be any regular electrical equipment in areas where flammable liquids are handled or stored.
“You need special electrical equipment — mortars, switches, wiring — that will not produce a spark. They’re specially classified for flammable vapour environments. If a regular switch costs $5, this kind of switch will cost $500. It’s much more expensive, but it’s absolutely necessary,” Fridlyand says.
The work area should have explosion-proof ventilation, lighting and equipment. The ventilation system must be good enough to reduce concentration of vapours to a safe level — that is, well below the flammable limit. The type and design of the system will be determined by factors such as the nature of the work, the types and amounts of products used and the size and layout of the work space.
“Any area where you’re working with flammable liquids should have either local exhaust or general dilution ventilation to prevent the buildup of vapours,” Hodgson says.
Workers also need to keep flammable liquids away from incompatible materials, substances that may react dangerously with a flammable liquid, generating excessive heat and possibly fire. For example, oxidizers, which release oxygen, will act to keep a fire going and make it worse.
Where there is a possibility of explosion, local codes may specify that the room or area has to be equipped with explosion-relief panels.
“These are part of the wall structure and made of a lighter material. They’re designed to be released at a certain predetermined pressure, and that prevents the collapse of the building. Otherwise, it would be like a bomb that would explode,” Fridlyand says.
Always dispose of rags soaked in flammable liquids in designated covered containers. Some flammable liquids, if left in waste materials, will slowly react with air and heat up enough to burn.
STORAGE OF FLAMMABLE LIQUIDS
When workers are handling small amounts of flammable liquids, the chance of a hazardous buildup of vapours is low. However, when liquids are stored, the quantities are larger and confined in a closed space, so the hazard from vapours building up becomes greater. Improperly stored flammable liquids can become a significant fire hazard. An undetected spill in a cabinet can also be dangerous.
“With these liquids, the more surface area there is, the more spread out the liquid is, the faster they evaporate. So, if you have a small opening in a bottle, it evaporates at a certain rate. If that bottle spills and ends up [spreading] over a square metre, it’s going to evaporate much quicker and create a more hazardous atmosphere,” Hodgson says.
Flammable liquids should be stored in areas that are cool, dry, well ventilated and away from ignition sources. They should be stored separately from incompatible materials.
These liquids are often transferred from their original container — a drum or tank, for example — to a smaller container. Use only approved portable containers that meet the safety requirements set out in the regulations and codes of the local jurisdiction.
There are several types of approved containers. Portable safety cans are a commonly used container and are designed for carrying, storing and dispensing flammable liquids. They have a spring-closing lid and spout cover, which automatically open when the vapour pressure builds up inside. This safety device prevents rupture (or explosion, in the event of fire). Containers should never be breakable.
Containers of flammable liquid should always be closed and properly sealed. They should be regularly inspected for damage and always have WHMIS labels attached before being stored.
Where there are larger amounts of liquids in a work shop or lab, the containers should be kept in flammable liquid storage cabinets. These approved cabinets are specially constructed and designed to protect the contents from fire and prevent the contents from contributing to a fire. Flammable storage cabinets should not be located near a room exit and must be labelled clearly, indicating that the contents are flammable.
It’s important to note that these cabinets are designed to protect their flammable contents from a fire — not to protect the people working nearby from the flammable vapours inside the cabinets.
“Many people get that wrong. The reason for this is, if a fire breaks out in your shop, lab or office and it reaches the flammable liquids, the liquids can enhance the fire quickly. Using these flammable cabinets buys you an hour or two hour, depending on the cabinet, and gives you time to evacuate before the flammable liquids are ignited,” Hodgson says.
EMERGENCY RESPONSE
Employers must conduct a fire risk assessment and develop a fire safety plan that covers proper safe work, storage, maintenance and housekeeping procedures and make sure workers are trained in these procedures, Besliu says. They must also provide clear instructions on how to handle spills and fires, covering topics such as the location of the fire extinguisher, alarm sounding, exit routes and meeting points. The workplace should have a readily accessible extinguisher.
“Workers must respond to a fire according to the procedures outlined in the fire safety plan. In general, the steps that should be followed are: Sound the alarm; try to extinguish the fire only if the fire is small, there is an appropriate fire extinguisher and you have been trained to extinguish a fire; if the fire cannot be controlled, evacuate, meet at the meeting point and wait for the fire department to control the fire,” she says.
It’s really important, Hodgson says, for workers to not remain on site and try to extinguish a flammable liquid fire they may not be able to control.
“People should not be heroes,” he says, adding that everyone should focus on preventing the liquids from igniting. “Everything we do — installing ventilation, minimizing the quantity we work with, storing the liquids properly — all these things are about preventing fires.”
Learn how fire blankets are effective tool for fire prevention, suppression, and compliance with fire safety regulations here.