Company wins gold in manufacturing category of Canada's Safest Employers awards
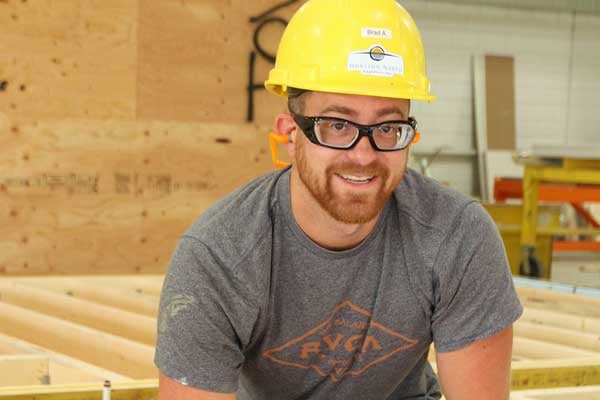
Behind the façades of many new hotels, commercial buildings and private residences is a growing industry — modular construction. Horizon North Modular Solutions, in 175,000 square feet of temperature-controlled manufacturing capacity in British Columbia and Alberta, produces sections of buildings that are transported to sites, set on foundations by cranes, assembled and integrated with building infrastructure. Completed modular structures look the same as those built by traditional construction methods, but are of higher quality, more cost-effective and environmentally friendly.
The 250 workers at the Kamloops, B.C. plant can produce 15 to 25 such units per week. This team sets the standards for safety and product quality not only for the in-house manufacturing operation, but also for outside subcontractors.
“One of our biggest challenges when we act as general contractors on a site is ensuring that subcontractors are integrated into our safety culture,” says Jorje Castellanos, vice-president, manufacturing and product development. “While as a public company we are under pressure to be profitable, everyone in our business has learned that we do not compromise on safety.”
Weekly one-hour safety meetings attended by the plant manager, safety manager, leads, supervisors and forepersons foster this integration.
“We discuss incidents and near-misses and how to prevent them in future — whether it’s in manufacturing, design or construction,” says Castellanos. “Doing this on a regular basis helps keep safety top of mind.”
Subcontractors are also required to complete health, safety and environment (HSE) orientation before starting work at a site.
According to Kelly Twist, manager, HSE, the growth of the business is constantly introducing new employees from various safety cultures into the mix.
“We have a big focus on orientation training for new employees followed by practical mentorship on the job,” she says. “And we have extended our training for everyone with an online portal for different learning styles.”
In addition, the company’s leadership safety audit helps build relationships between leaders and employees by either educating workers on unsafe acts or celebrating safe ones.
“This is especially effective with new workers, since it engages them in a two-way conversation and builds trust,” says Twist. “Leaders spend about 30 per cent of their time on the plant floor, where they check in with those employees and follow up on the talks.”
Twist reports that two annual safety campaigns have led to greater safety engagement, awareness and positive changes. The first, Line of Fire, covers impact incidents.
“Keeping out of the line of fire — impacts from equipment such as saws and nail guns — involves being aware of your body positioning and knowing how and where to deal with safety hazards,” says Twist.
The second campaign is Get a Grip, which focuses on slips, trips and falls.
Both campaigns have resulted in related incidents being drastically reduced over the last several years. They have been so successful that many of Horizon North’s clients have adopted the programs as well.
“Campaigns are also framed so messages are easy to take home and share with the family,” adds Twist.
A popular visual safety reminder is Safety Syd, an illustration representing a gender-neutral worker with red and yellow stars on its body where first aid or recordable injuries have occurred. Each site has a large poster of Safety Syd and, when necessary, staff are involved in placing the stars, followed by a discussion of how the injury could have been prevented.
Despite a rising employee count and other challenges, the Kamloops plant’s workers’ compensation board premium is at 1.06 — considerably lower than the overall manufacturing rate of 1.73.
“Strong company leadership underlines our robust safety culture,” says Twist. “Working at Horizon North is a lifestyle choice — and everyone knows what the expectations are.”