Tips to create a safety system that works now and into the future
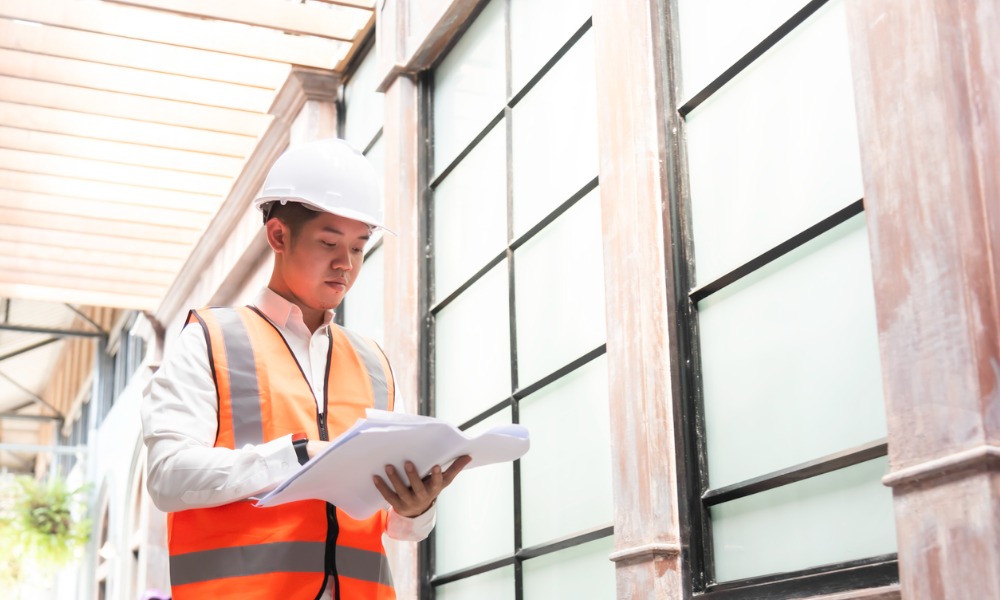
Making the workplace safe for employees and customers should be a priority for every business. Many industries believe that because they do not have obvious physical hazards, they do not need to be as concerned about health and safety. In an industry such as construction, for example, safety hazards are more obvious which makes them easier to prioritize. Every organization, from manufacturing and retail to food services and the public sector, must comply with safety guidelines and consider potential risk factors for injury and illness in their workplace.
A risk assessment is not mandatory to meet Occupational Health and Safety (OHS) requirements, however it can be an important step in your overall Health and Safety Management program to assist in keeping your workplace and employees safe. A risk assessment provides a valuable guideline to help you comply with Regulations and Guidelines in every industry. Many businesses do not prioritize risk management in their processes, either because they do not think it is necessary or because there are certain challenges associated with completing one. This article will seek to identify those challenges and introduce some strategies for performing successful risk assessments for your business.
The basics of safety risk management
Risk evaluation in a business is a proactive approach to mitigating risks rather than a reactive approach. It involves more than simply walking through a workplace identifying potential sources of injury or accidents and is instead the active and on-going process of prioritizing potential hazards based on significance to operations and potential for employee/customer injury.
After identifying potential risks and creating a prioritization list of risk areas that need to be addressed, risk evaluation involves mitigation. Organizations must determine control measures that can be used to reduce or eliminate risks and turn them into safety-driven areas. For example, in the construction industry, a common safety risk is the operation of machinery or tools. Tools and machinery that are poorly maintained can lead to breakdowns and increased physical demand, damage to the site, or injury to employees. Proper maintenance and training procedures would be a top priority. As part of risk mitigation, you would seek to find ways to control or eliminate potential hazards in this area to ensure the risk does not translate to damage. One way to reduce risks would be to implement regular inspections and safety checks on the machinery and invest in employee safety training. By doing this, you reduce hazards which also serves to mitigate potential future financial, mental, and physical consequences using the basics of safety risk management.
Challenges facing risk management
There are several organizational challenges involved in implementing risk assessment as part of your OHS program. Ideally, risk assessments would be completed prior to start-up as this is more cost effective and less dangerous than reacting to risks later on. Facing risk assessment challenges head-on is essential.
- Operational Interruptions
Some business leaders feel that taking time from their daily operations to run safety checks and risk assessments will keep them from being as productive as possible. However, injury and damage will cause much more interruption than regular risk assessments and are worth the time investment.
- Cost Considerations
Some companies avoid risk assessments because they think the assessment itself will be expensive or mitigating the risk areas will be expensive. However, the alternative to risk management is waiting until accidents occur. This reactive strategy can cause costly damage to the business or potentially hurt employees or customers. Taking on a small cost now helps businesses avoid larger costs in the long run.
- Employee Communication
Risk management is an active process involving employees at every level of the organization. As a health and safety professional or business leader, it can be difficult to get a clear picture of every potential risk area in the organization, yet many employees are not actively involved in the risk assessment process. Opening communication channels for employees can help expand risk management by identifying areas of improvement throughout the organization.
- Inexperienced in Risk Planning
Some managers and business owners have been operating their business the same way for a number of years and are simply inexperienced in risk management and how to undertake a safety risk assessment in their organization. This challenge can be addressed through the strategies outlined below.
Increasing success in safety risk management
Gary Cohn, famed philanthropist, and business leader, says, "If you don't invest in risk management, it doesn't matter what business you're in, it's a risky business." Avoiding risk entirely is almost impossible, but choosing not to prioritize and plan for potential risk areas will allow those risk areas to grow and accidents to happen. Your business is in danger, even in small ways, every day, and risk management can help you keep it, your employees, and your customers safe. There are many different strategies for improving your risk management process.
Walk the floor
Many organizational leaders need help with high-level planning. Thinking about your company's long-term goals is important, but if it prevents you from "walking the floor" of your organization you will not be able to engage in risk management. Anyone thinking about organizational risk must be on the ground in their company, talking with employees and physically looking at different areas of potential hazards.
Create a plan
Every organization successfully implementing risk management starts with a plan. A risk management plan allows you to build out potential risk areas and identify how you will prioritize and improve or eliminate risks.
Designate a team
Risk management is an active process and should involve many different organization members at all levels. Everyone has a unique perspective on risk in their own operations and in terms of resolving risk areas. Collaborating with a team of people is important to ensure you have the most comprehensive view of potential occupational risks.
Work with professionals
Occupational health and safety professionals play a critical role in ensuring workplace safety and helping with risk management. From keeping operations compliant with safety guidelines to emergency training and safety assessments, these trained professionals can identify and find solutions for potential workplace safety issues. They can come into your organization and implement positive changes in an effective way. Working with qualified and experienced professionals can help increase your risk management success.
Use safety training
Everyone should be actively included in avoiding risk. Once you know your potential risk areas, an important next step is to complete safety training for your employees in the specific areas. A risk management plan will not be successful if your employees are unaware and not actively participating.
Ongoing risk management
After mitigation measures have been implemented, your job is not done. Regularly evaluating organizational risk is vital to ensuring long-term risk management operation. Open lines of communication with employees and allowing them to report potential new and recurring risk areas are critical to on-going success. Schedule regular meetings and walk-throughs to ensure you are aware of organizational risks at all levels of operation and that identified targets, goals or outcomes are being achieved.
Organizational risk management is a challenge for every industry. The very idea seems difficult to grasp at times; you are attempting to see the future of every area of your organization and what potential there is for injury or damage. However, you do not need to be able to see the future to manage risk in your company properly. If you proactively plan and use past experience and data to help you predict future organizational risks, examine industry trends and resources, use on-the-ground observations to determine the potential risk areas are within your organization, and actively work to mitigate those risks every day, you can increase your company's overall safety.
Kylie Boyd
Kylie Boyd, M.Ed., is an Instructor of Health and Safety Management at Kompass Professional Development, a division of Herzing College. Kylie is an accomplished and dedicated professional with extensive operational and leadership experience in project management, health and safety and the instruction of health, safety, and wellness.