Signs that use LED and laser light may help raise hazard awareness and combat complacency
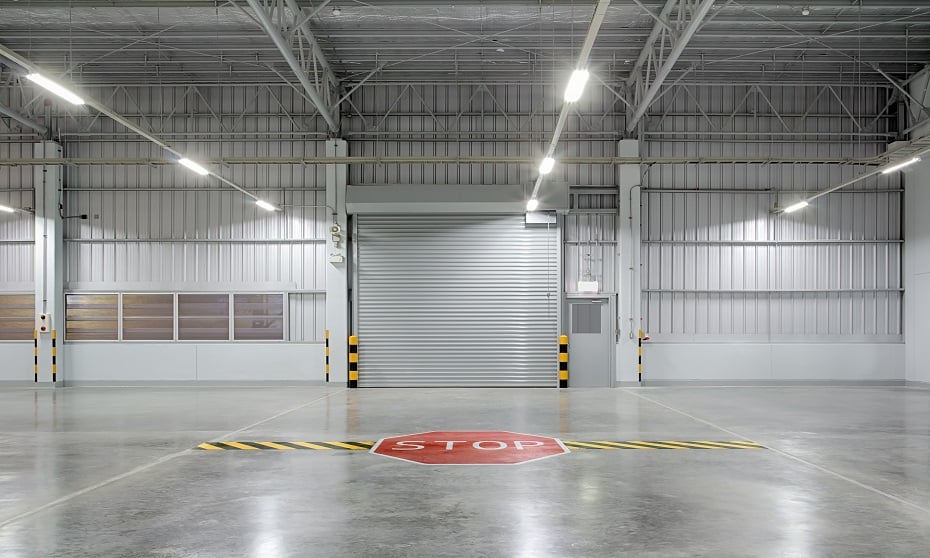
In May 2013, a worker in a meatpacking plant in Ontario was operating a forklift when he collided with material being moved by a co-worker. The worker suffered a broken ankle. Four years later, the company, Concord Premium Meats, was found guilty of violating the province’s Industrial Establishments Regulation and fined $55,000. Among the violations was the failure “to ensure barriers, warning signs or other safeguards for the protection of all workers were used where vehicle or pedestrian traffic may endanger the safety of any worker.”
Safety signs are an essential feature of industrial work sites, where workers are in constant proximity with heavy machinery and vehicles. Traditionally, safety warnings and directives have been communicated to workers by painted or adhesive signage on floors and walls. In the last few years, new light technologies have led to a completely different kind of signage. Projected images may be set to replace conventional, fixed signage.
“We have the ability to change and create any kind of signage,” says Atul Garg, vice-president of operations at Toronto-based Laserglow Technologies. “Any kind of signage there is in the industrial space, we can create those using our projector-based technology.”
In a basic setup, a projector — mounted overhead on a beam in the ceiling — projects an image down onto the floor. Projectors consist of three main elements: the projector body, image template and lens angle.
Projectors today tend to be highly durable. According to an international enclosure rating system, most are rated IP65, indicating the units are sealed off from dust and dirt and are protected against water projected from a nozzle — a hazard in food-processing sites.
The image template determines the image to be displayed on the floor. Similar to a photographic slide, it can be changed out for another image when needed; for example, if the layout of the warehouse changes. Signs can range from standard warnings, such as “Slow” or “Fire Extinguisher,” to more customized messages, such as “Safety Shoes Required” or “Eye Protection Area.” The template is often called a gobo, or “go before optic.”
The lens angle goes in front of the image template and allows the user to focus the image on the surface where the image is to appear. Different types of angle lenses can be put on the projector to increase or decrease the size of the projection.
Projected signage systems are intended to be plug-and-play, so generally no training is needed to handle them. A maintenance worker or person with basic electrical knowledge should be able to install and operate the system.
The use of projected safety signage, made possible by the development of the 300-watt LED projector, began about four years ago and has greatly accelerated in the last two to three years. There are two different projected systems: one based on LED technology (light-emitting diodes); the other on laser light. Recent advances in light technology have made it possible to produce bright, colourful, clear and crisp imagery onto a factory floor, says Mark Wray, CEO of Old Hickory, Tenn.-based LTBLtech.
“And the image doesn’t degrade. No matter what is on that floor, no matter the condition of the floor, no matter how much transportation goes across that image, the quality of that image will remain exactly the same from the time it is deployed until the light engine dies — and depending on the harshness of the environment, that light engine can survive anywhere from 14,000 hours up to 40,000 hours,” he says.
APPLICATIONS
Most often, projected signage is used to display traffic control signage on walls and floors in high-traffic areas. Typically, these signs have warnings such as “Stop,” “Yield” and “Danger Forklift Traffic.”
“The most common problem in these areas is forklift traffic and pedestrian traffic. There are many accidents there — where the forklifts don’t see the pedestrians and run into them or the pedestrians walk into these aisles where the forklifts are supposed to be driving,” says Uli Theissen, CEO and owner at Scotts Valley, Calif.-based GoboSource Projection Systems.
Safety managers can also use projected signage to replace painted or taped pedestrian-safe aisles, using either projected LED or laser light. Overhead projectors casting bright LED light can be set up to create two thick, coloured lines along the floor. Projectors can also be used to create the familiar, solid-colour or striped walkway. For long walkways, more than one projector is needed.
Alternatively, high-intensity lasers can be used to produce virtual lines along floors and other surfaces to demarcate pedestrian lanes and other zones, such as staging areas where pallets or equipment are supposed to go. By installing two overhead lasers that project parallel lines or stripes along the floor, a manager can create a safe lane or walkway. If the lane is beside a wall, only one overhead laser may be needed to create the lane. Virtual laser lines are also used to create lanes to guide truck drivers into warehouses, helping them stay in their designated lanes and away from pedestrians.
“The lasers are very efficient; they can generate a very long line with a single laser,” Theissen says. “The lasers used in these environments are classified as laser class 3R, so they are absolutely eye safe. You can look into the laser beam without any problem.”
Projected signage can be used on overhead cranes. The projector casts coloured lines or spots onto the floor below to warn of a suspended overhead load. Projectors can also be mounted on forklifts where they project lines, spots, arrows or warning signs to indicate the vehicle’s approach. This application is suited to areas where alarms are difficult to hear.
While projected signage works best in indoor environments, it can be used outside, too. The challenge is that when light technology goes outdoors, it usually becomes invisible in sunlight. To be visible on bright days, the power of the projected light must be very high, and with lasers, that light intensity would need to be so high that the laser would no longer be eye safe.
However, there are products used outside. For example, a projected laser-line system developed by LTBLtech that creates pathways for docking trucks projects laser lines and safety signage inside and outside. It was designed for use in northern workplaces, where snow and ice often obscure outdoor lines. The green and red lines are visible only when there is no bright sun.
ADVANTAGES
One of the main advantages of projected signage is that, unlike paint and stickers, the signs don’t wear off. As a result, companies are saved the cost, effort and downtime required by constant replacement, Garg says.
“Stickers and paint wear quickly and need to be constantly replaced. In high-traffic environments, that can be as often as every three weeks to every six weeks. To replace stickers, you have to cordon off an area and close operations. If you’re painting, you have to cure the surface, strip the old paint, lay the new one, let it dry. So, there’s lost time and productivity,” he says. “With projected signage, the projector is mounted overhead. No wear and tear can ever happen because there’s nothing on the floor.”
The safety advantage of projected signs, Garg adds, is that they are more effective at drawing attention to workplace hazards than fixed signs, which become part of the landscape and are soon ignored. Bright colours make projected signs highly visible. The use of motion sensors can also help alert workers to the signage.
Motion sensors, beam break sensors or push buttons can be used to trigger projectors to begin displaying a sign or start flashing a normally steady sign. For example, a motion sensor may detect a forklift approaching a walkway and will prompt warning signs to appear on the floor in front of any pedestrians who may be on the walkway. A sensor may detect a person opening a door and instantly project a safety image onto the floor.
“The biggest advantage of projected signs over stickers is their dynamic nature. In this technological age, people don’t pay attention to signs around them. People are always on their phones. Complacency happens to all workers,” Garg says. “When motion is detected, [a manager] can have the signage come on and flash at a certain rate. All of a sudden, there is a change in the environment; the human eye picks up that change and you are made more aware of a potential hazard in the workplace.”
Projected signage can be used in most environments, but it is particularly useful in high-traffic areas, where paint and adhesive signs wear off and damage quickly; in safety-critical areas, where signs must be visible; in dark areas, where paint is hard to see but light is very visible; and in dusty, dirty or wet areas, where painted and taped signage deteriorates fast.
“The most common industries currently buying [projected signs] are in the automotive sector, the steel and lumber industries and the foodprocessing industry,” Garg says. “But any place that has a sign can use a virtual sign.”
DISADVANTAGES
While she thinks projected signage is in some ways a great concept, Julie Tilley, safety professional at Calgarybased Workforce Compliance Safety, says constantly changing signage is more likely to decrease workers’ adherence to safety messages.
“In industrial settings, consistency is the key. Someone who sees a stop sign somewhere every day of their life is going to stop. If they just see it once in a while, they may not,” she says. “If you drive and every day you see a stop sign somewhere and you know you have to stop, then whether the sign is covered in snow or someone has knocked it down you’re still going to stop. It’s a habit, and you know it’s the right thing to do.”
Moreover, Tilley adds, there is a risk of workers coming to rely on a suddenly appearing image to warn them of a serious hazard. Yet, unlike fixed signage, the need of a power source makes the system vulnerable to problems, and there may be technical failures, such as a projector or sensor malfunctioning. A preferable solution may be combining the fixed sign, which workers are always required to observe, with a projected sign that comes on flashing when a hazard is imminent.
Concerning maintenance, she says the life of fixed painted signs can be greatly extended by the use of durable, industrial paint. For example, highgloss alkyds and epoxy paints are estimated to last three to five years. Applying a sealant over the paint can also make signage last longer.
COST COMPARISON
In relation to painted or taped signage, which requires frequent maintenance, projected technology makes for cost-effective signage, Theissen says. In high-traffic areas, the one-time cost of projected signage ranges from $500 to $6,000, while paint or adhesive signage can cost $1,000 to $4,000 annually.
“And, often, it is actually a much higher cost because, if you re-paint a whole intersection, traffic there is stopped for a day. There is a major disruption in the production process, and that means additional cost, and it’s hard to measure that,” Theissen says. “Typically, for a high-traffic area, the return on investment of a projected system is two to three years.”
With advanced light technologies, companies are experimenting with new uses for projected signage. GoboSource, for example, is working on a pilot project in Alberta that involves projecting crosswalk signage onto the road at a traffic intersection near a school. The goal is to maintain visible signage even in the winter.
“The signage is always on. When it snows, the signage would not normally be visible. But a projected image can be projected onto the snow and will always be visible,” Theissen says. “It will make sure the cars stop for the kids.”
This article originally appeared in the March/April 2020 issue of COS.
ENSURING EFFECTIVENESS OF SIGNAGE
- Viewing distance (Is the worker close enough to the sign to read it?)
- Illumination (Is there enough light on the sign?)
- Legibility (Are the words and images readable? Are they obscured in anyway?)
- Clarity of the message (Can the worker understand what the words mean?)
- Conspicuity and placement (Does the sign capture the worker’s attention?)
- Image details (Do the images clearly show the danger of certain actions?)
- Reading time (How long will it take the worker to read the sign?)
- Visual acuity (Is the worker’s eyesight good enough to read the sign?)
- Perception factors (Does the worker have the background knowledge to understand the sign?)
Source: WorkSafeBC
COMMON USES FOR PROJECTED SIGNS
- RUGGED CONDITIONS Used in wet, cold, humid or dusty environments
- HIGH-TRAFFIC AREAS Projected signs are not affected by foot and vehicle traffic
- HIGH-RISK AREAS Motion sensors can be used to warn personnel as they approach high-risk areas
- ON MOVING EQUIPMENT Projectors can be installed on cranes and forklifts
- LOW-LIGHT ENVIRONMENTS Projected signs are highly visible in both bright and low-light environments
- TO COMBAT COMPLACENCY Blinking or rotating signs increase awareness
Source: GoboSource