Strategic solutions manager Nick Bixcul of Kee Safety points to crucial steps towards preventing industrial accidents
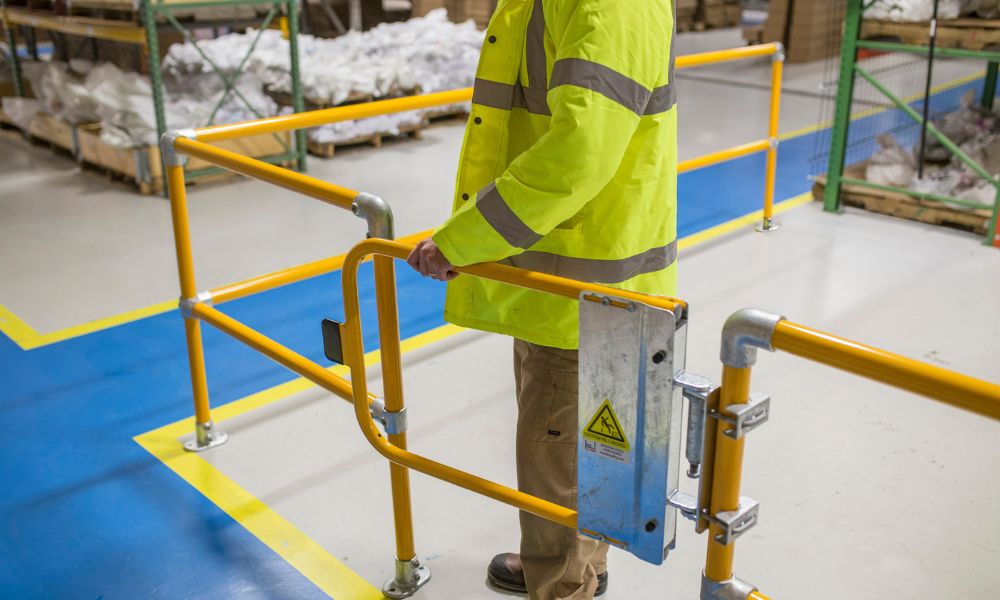
This article was produced in partnership with Kee Safety.
Safeguarding employees in a manufacturing workspace
Strategic solutions manager Nick Bixcul of Kee Safety points to crucial steps towards preventing industrial accidents
Collapses, chemical mishaps, and explosions can all result in traumas such as fractures and cuts, as well as accidents involving heavy machinery within manufacturing facilities. These incidents are not only potentially lethal for workers, but also come with significant financial burdens for employers, such as workers' compensation, legal expenses, penalties from regulatory bodies, costs related to employee turnover, reduced productivity, and expenses for repairing or replacing damaged equipment. A single mishap can wreak financial havoc on a business.
To prevent industrial calamities, protect your personnel, ensure adherence to manufacturing regulations, and safeguard your financial interests, prioritizing safety is paramount.
Kee Safety’s strategic solutions manager, Nick Bixcul maintains, “Workplaces, especially facilities or manufacturing plants, come with their own set of hazards such as pinch points and the potential for serious injuries like impalement if one tries to squeeze through tight spaces. The environment plays a significant role in determining the risks associated with a particular workplace.
“When assessing workplace safety, one of the primary considerations is the paths people take from point A to point B. Just because a particular route has been designated doesn’t mean it’s the route people will take, nor does it guarantee it’s the safest or best option available. It's crucial to continually evaluate and ensure that the established routes are indeed the safest for everyone involved.”
Manufacturing safety encompasses all measures taken by an organization to preserve the well-being of employees in a manufacturing setting. This involves multiple aspects, including personnel, procedures, and technology:
- Personnel must prioritize their safety and that of their coworkers by staying informed about safety protocols, adopting safe work practices, and proactively addressing hazardous conditions.
- Business operations must be structured around safety. This includes all policies, tasks, routines, and decisions made by leadership or management, with a focus on minimizing risks and fostering a culture of safety.
- Technology should enhance safety by ensuring that machines used by workers are designed and installed with safety considerations. Every technological tool should aid in safeguarding individuals rather than posing risks.
Manufacturing safety enhances productivity by reducing accidents and their associated disruptions. It also serves as a key aspect of risk management, mitigating liabilities arising from dangerous machinery, behaviors, and processes.
It is crucial to understand that safety and profitability are closely linked, with safer companies generally outperforming and outlasting those that are not as safety conscious.
The cost to safety
Bixcul says, “Some simple yet effective safety measures include installing safety gates to control traffic flow and using barriers and guardrails. This includes access and egress points, as well as protective measures for specific locations. Barriers or complex Lifeline systems are examples of measures that can be implemented to address these concerns. Safety rails play a crucial role in keeping people at a safe distance from machinery and other equipment. These barriers act as the first layer of protection, preventing accidents and injuries by physically separating people from potential hazards. Implementing these measures is a proactive step towards creating a safer work environment.”
The cost of ensuring a safe working environment can be perceived as a significant investment, particularly when compared to other expenses.
Bixcul reveals if a company is willing to invest a substantial amount of money, say $1,000,000, in procuring a new piece of machinery, one would assume that they would also prioritize the necessary safety measures, such as a $5,000 or $10,000 railing or barrier system. However, this is not always the case. The financial outlay for safety measures may seem disproportionate when compared to the cost of the machinery itself.
There can be a tendency to assume that existing plans or structures, especially those that have been in place for a considerable length of time, should already incorporate the required safety features. This cannot simply be assumed. It's important to recognize that safety standards and regulations can evolve over time, and what was considered adequate 50 years ago may no longer be sufficient.
The primary responsibility of safety system manufacturers is to create products that safeguard workers and prevent injuries in the workplace. “My role goes beyond simply closing a sale or securing a project,” says Bixcul. “My primary responsibility is to protect individuals from potential hazards, whether that involves designing out risks or taking other necessary measures. Even if it doesn't result in a sale, the most crucial outcome is ensuring the safety and well-being of people so that they can return home safely to their families. It is vital that both the places people go to and return from are secure and free from harm.”