As economic pressures mount, Toyota Motor Manufacturing Canada's safety is using tech to reinforce its human-first philosophy, not replace it
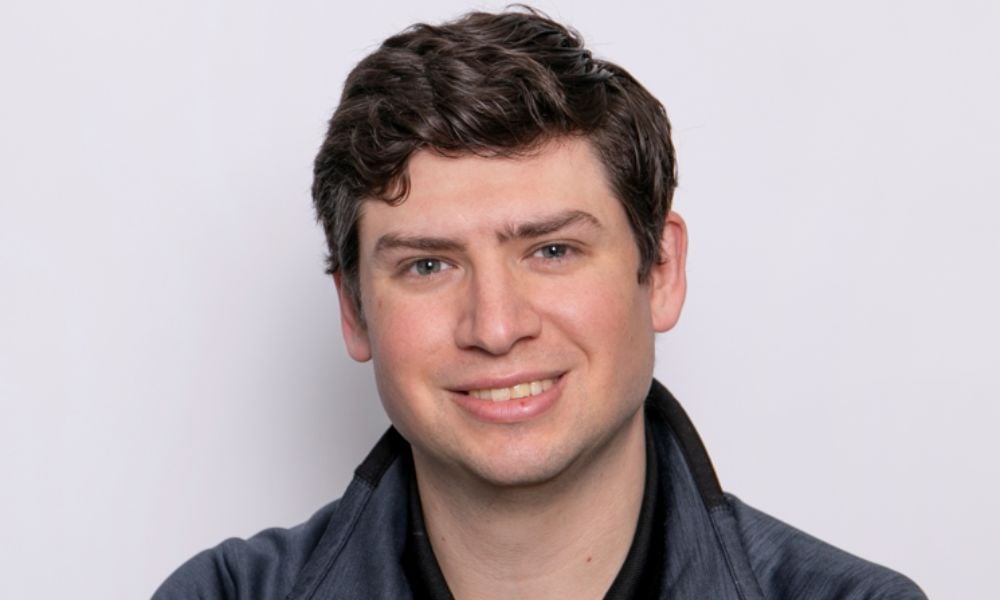
Toyota Motor Manufacturing Canada (TMMC) is doubling down on a long-standing principle: no innovation or efficiency is worth compromising worker safety. While many manufacturers race to automate, they’re taking a slower, more thoughtful path—using AI to reinforce, not replace, its safety culture.
Global logistics disruptions and economic pressures have pushed automakers toward rapid digitization. Yet according to the International Labour Organization, nearly 2.3 million people die each year from work-related accidents or diseases—a figure that AI promises to reduce, but only if implemented with caution. For TMMC, that means embedding AI into its safety programs without cutting corners, compromising ergonomics, or sidelining human oversight
Seth Burt, Safety Manager at TMMC, is at the helm of this effort. Focused on long-term thinking and people-first design, he sees AI not as a buzzword but as a tool to fortify—not fracture—safety foundations. “Safety can't be the casualty of this efficiency,” he says. “TMMC’s focus has always been long-term commitment and thinking for the future.”
“With TMMC, AI can be a resilient tool,” Burt adds. “We’re still on the cusp of understanding what it can do, especially when it comes to maintaining safety standards during rapid changes.”
AI’s role: a partner, not a replacement
While many companies scramble to respond faster to disruptions, Burt emphasizes that insightful response matters more than sheer speed. Emerging technologies often move faster than the regulations meant to govern them, and TMMC is investing in AI systems like computer vision and machine learning to fill that gap—monitoring real-time conditions even as production layouts shift.
“They can detect unsafe conditions and behaviors, even when the layout or workflows change due to substitutions of part changes or storage changes,” he explains.
TMMC’s approach ties closely to its rigorous model change cycles, driven by customer demands and market shifts. Here too, AI is finding a role.
“We go through quite the rigorous cycle of model changes… AI can help us analyze near miss data or correlate with any other kind of production adjustments,” Burt says. “There’s a lot of potential there, allowing for proactive interventions rather than reactive ones.”
Still, Burt is clear: no matter how sophisticated the tools get, they are meant to complement—not replace—the expertise of human safety professionals.
“We believe automation should enhance, not replace, the expertise of our safety professionals,” he says.
Designing technology around people
That philosophy runs deep. Burt warns of the dangers of designing around machines instead of workers, a misstep that can introduce entirely new hazards.
“If we automate without some sort of human-centric design, we risk creating new hazards or blind spots,” he explains.
To prevent that, TMMC integrates its ergonomists early in automation planning, ensuring that any technological introduction—from collaborative robots to new workstations—centers the needs of workers first.
“We can use AI tools and digital tools to simulate process, postures, reach zones, fatigue levels,” Burt says. “But our ergonomists, who interpret the data in the context of real-world variations, are very vital in the entire procedure.”
That human-first approach shapes broader innovation efforts across the company. Guided by the Toyota Way, with its pillars of “Continuous Improvement” and “Respect for People,” we demonstrate our respect for our Team Members by providing a safe work environment.
This is ongoing and active through key engineering, production, and safety teams together to collaboratively rework processes—balancing safety, ergonomics, quality and productivity in every decision.
“This ensures that automation decisions consider ergonomics in both safety and productivity,” Burt explains. “It reflects our core value of respect for people.”
Long-term thinking over short-term pressure
Toyota adapts to customers needs and desires and with that comes rapid changes and with rapid changes comes risk in all levels of the operations including Safety and Ergonomics.
But the company still upholds its rigorous auditing process, compressing the Plan-Do-Check-Act (PDCA) cycle without cutting corners.
“We’re compressing that PDCA cycle—the plan, do, check, act—without skipping the necessary steps, especially the element of check,” Burt says. “We have many audits and inspections to ensure we maintain safety compliance especially post implementation of any program, equipment or process”.
For Burt, clear regulations and human oversight are more important now than ever. He calls on industry bodies to step up, warning that without firm standards, economic pressures could erode safety culture.
“Regulatory industry bodies and partners must lead with clear, proactive guidelines on AI usage and safety, ensuring support now replaces due diligence,” he says.
He also highlights the ethical dimensions of AI adoption—from protecting worker data to guarding against algorithmic bias.
“Safety isn’t just a compliance issue—it’s a moral one,” Burt explains. “When economic pressures rise, clear regulatory expectations become more important to prevent shortcuts and reinforce long-term thinking.”
TMMC’s own history with new technologies, like exoskeletons, offers lessons for the AI era: move forward, but move carefully. Burt stresses that understanding a technology’s limits is just as critical as embracing its potential.
“What is the potential, what can it do, and what can it not do?” Burt says. “It’s really important to evaluate in both perspectives—and not get too overwhelmed and excited over all the potentials without the considerations of any sort of limitations.”