How a robust safety system can directly contribute to the credit account of your company
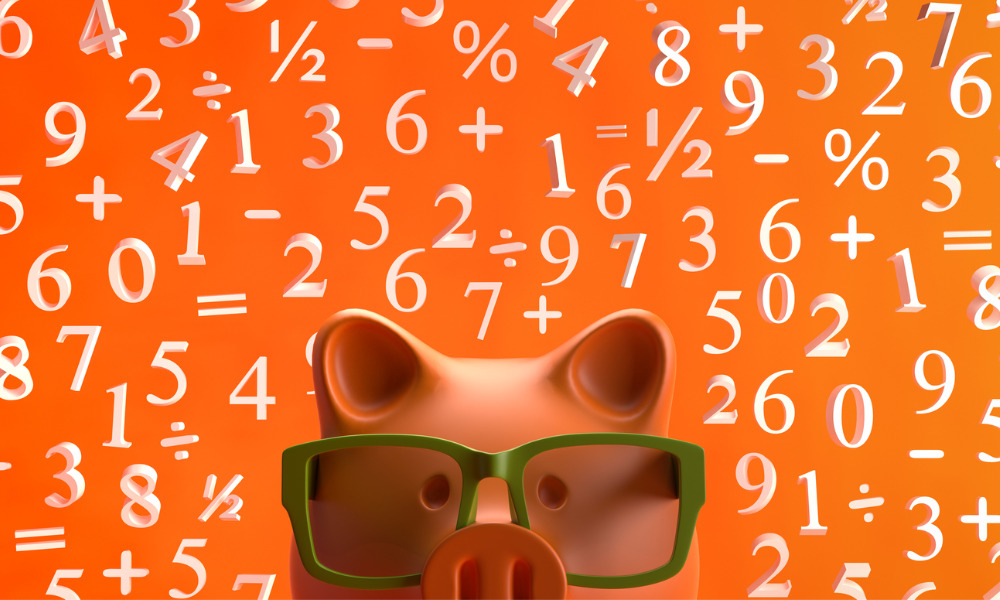
Most employers, if not all, in Ontario show utmost commitment to the health and safety of their workers by not only implementing various benchmarked Occupational Health and Safety (OHS) management systems/program standards but also establishing a loyal partnership with the Workplace Safety and Insurance Board (WSIB). With a goal to zero work-related injuries or illnesses, WSIB has been providing no-fault collective liability insurance to organizations. At the same time, for many organizations, one of the big parts of their OHS budget goes towards WSIB premiums.
The challenging part for most safety professionals is to reduce the budget without compromising the health and safety of the workplace. There are many ways safety professionals can think to minimize unwanted costs without compromising safety, for example optimizing residual risks using as low as reasonably practicable (ALARP) principle, negotiating existing contracts, exploring new vendors, etc. However, there is very little room for cost-cutting in an already established robust OHS system, especially where reputed management systems/program standards are in place.
But don’t worry, there is good news! You can save a lot of dollars by using your existing system, thanks to the WSIB!
Before going into how we can save, let’s first find out the commonality between various reputed OHS management systems/program standards. Although this discussion revolves around Ontario workplaces, one can very easily find out similarities with other systems/standards as well from the below.
Harmony between Different OHS System:
Before a detailed discussion, let us discuss a very common project management tool, Plan-Do-Check-Act i.e. PDCA Cycle. This is a four-step repetitive tool for continuous improvements.
Plan- Formalize the goal/products/KPIs and then outline the processes to achieve those. The more robust the plan is, the more chance of success.
Do- Perform and implement the planned processes
Check - In this stage, continuously monitoring, recording data, and evaluating the outcomes with the expected results are primary goals. It starts from the ‘Do’ stage and repeats multiple times till you reach optimal solutions by continuous improvements.
Act - This stage involves unearthing corrective and preventive actions for the issues/findings from previous stages and implementing them.
Planning for the next cycle could have better goals/products/KPIs and the cycle would re-start then.
ISO 45001:
ISO 45001 is an OHS management system (OHS MS) by the International Organization for Standardization (ISO), a worldwide federation of national standards bodies. This standard aims to remove hazards and reduce OHS risks by implementing effective preventive and corrective measures in workplaces, hence stopping work-related injury and illnesses. Sounds familiar? Yes, this is almost similar to the WSIB’s goal.
ISO 45001 contains the following 10 clauses:
- Scope
- Normative references
- Terms and definitions
- Context of the organization
- Leadership and worker participation
- Planning
- Support
- Operation
- Performance evaluation
- Improvement
Let’s see how it is in-lined with the PDCA Cycle. Clause 1, 2, 3, 4, and 6 helps to create the Plan stage. Clause 7 and 8 build the Do stage. Clause 9 and 10 shaped the Check and the Act stages respectively. Whereas Clause 5 remains involved with all the four stages.
CSA Z100:
As stated by the Canadian Standard Association (CSA), the purpose of this standard is to specify the requirements to protect workers’ health and safety and optimize OHS performance in workplaces. Again, the goal is very similar to the above. Let’s see the sub-clauses of the OHS MS Clause i.e. Clause #4.
4.1 General
4.2 Commitment, leadership, and participation
4.2.1 General
4.2.2 Management commitment and leadership
4.2.3 Worker participation
4.2.4 Occupational health and safety policy
4.3 Planning
4.3.1 General
4.3.2 Initial review
4.3.3 Legal and other requirements
4.3.4 Hazard identification and risk assessment
4.3.5 Occupational health and safety objectives and targets
4.4 Implementation
4.4.1 Infrastructure and resources
4.4.2 Preventive and protective measures
4.4.3 Emergency prevention, preparedness, and response
4.4.4 Competence and training
4.4.5 Communication and awareness
4.4.6 Procurement and contracting
4.4.7 Management of change
4.4.8 Documentation
4.5 Evaluation and corrective action
4.5.1 General
4.5.2 Monitoring and measurement
4.5.3 Incident investigation and analysis
4.5.4 Audits
4.5.5 Nonconformities — Preventive and corrective action
4.5.6 Evaluation of compliance
Here, sub-clauses 4.1 to 4.3 help to create the Plan stage whereas sub-clause 4.4 takes care of the Do part. Then, sub-clauses 4.5.1 to 4.5.4 guide to the Check phase, and 4.5.5 and 4.5.6 to the Act phase. Moreover, Clause 5, i.e. Management Review and continual review, could be a part of all the phases or to re-start a new cycle.
WORKWELL PROGRAM:
This program helps to prevent injuries/illnesses/fatalities/occupational disabilities by improving OHS and return to work (RTW) programs.
Workwell standard consists following twelve elements:
1. Policy Statements
2. Senior Management
3. Health and Safety Responsibilities
4. Posted Health and Safety Materials
5. Health and Safety Standards & Procedures
6. Health and Safety Representative/ Joint Health and Safety Committee
7. Health and Safety Education/Training
8. First Aid Requirements
9. Health and Safety Inspections
10. Preventive Maintenance
11. Incident Investigations
12. Return to Work
At first glance, one can feel that the PDCA principle is not that evident although few of the elements could be correlated with it, for example, elements 1 to 6 & 8 would help to create with the Plan stage, and 7, & 9 to 12 could be with the Do part.
Here is the catch. First and foremost, this program is very nicely structured. Here a few elements (e.g. elements 1 to 3) clearly contribute to the single stage i.e. the Plan stage, whereas other elements are structured with the PDCA cycle itself, for example. Let’s consider element #12 i.e. Return to Work (RTW).
A written policy and program with defined responsibilities for both workers and management (12.1(a) RTW Policy, 12.1(b) RTW Coordinator, 12.1 (c) RTW Roles & Responsibility), how the activities will be carried out (12.1(d) Program Requirements, 12.1(e) Accommodations options, 12.1(g) RTW Plans, 12.1(h) Reporting Requirement to WSIB), and outlining the required documented information (12.1(f) Standardized Forms and Tools, 12.1(g) RTW Plans) will help to set up the Plan stage. The Do stage is the actual implementation of the planned program (12.1(j) Communications and Training) and could be easily tracked by interviewing employees and reviewing the records. The Check stage is being clearly emphasized at 12.1(d) (Independent assessment,), 12.1(k) (evaluations of plans, duration, and budget), and then Act stage at 12.1 (k) by asking improvement of opportunities and continuous improvement.
Therefore, the whole Workwell standard is nicely based on the PDCA Cycle.
COR and COR-2020 PROGRAMS:
As per the CFCSA (Canadian Federation of Construction Safety Associations), the Certification of Recognition (COR) program is a national accreditation standard that ensures a complete implementation of the OHS Management System with objectives to reduce incidents, accidents, and injuries as well as their associated human and financial costs.
The Infrastructure Health & Safety Association (IHSA), a member of CFCSA, has recently declared that the COR program was enhanced to COR-2020 to help interested workplaces qualify for financial rewards and recognition from the Ontario Government and WSIB, ON, as well. In this process 19 elements (13 common to all plus 6 supplemental for Ontario), the audit tool from the earlier COR program was reduced to 14 elements in the new standard and also incorporated new requirements that are in line with ISO standards.
In the previous COR Program guideline, IHSA clearly stated that it accepts OHSAS 18001 (Occupational Health and Safety Assessment Series, a precursor of the ISO 45001) which is again based on the PDCA cycle as an equivalent to the COR Audit. Moreover, COR-2020 Standard declared in its introduction that this is based on the PDCA framework. Looking at the former 19 elements and now the new 14 elements, both frameworks were clearly developed in accordance with the PDCA Cycle. Let’s discuss the 14 elements in the COR-2020 program.
5.1 Health and Safety Policy
5.2 Hazard Assessment, Analysis, and Control
5.3 Controls
5.4 Procurement and Contractor Management
5.5 Company Rules
5.6 Personal Protective Equipment
5.7 Preventative Maintenance
5.8 Training and Communication
5.9 Workplace Inspections
5.10 Investigations and Reporting
5.11 Emergency Preparedness
5.12 Statistics and Records
5.13 Legislation and Other Requirements
5.14 Management Review and Management of Change
Here, clearly, elements 5.1 to 5.11 and 5.13 will help to create the Plan stage and implement the Do stage. Element 5.12 and 5.14 will help to evaluate i.e. the Check step and the Act step, implementing action items respectively.
Hence all the above management systems/ standards were evolved through the PDCA cycle.
The New Opportunity: Health & Safety Excellence Program, WSIB
As per WSIB, it integrates the strength of its previous voluntary programs (Small Business, Workwell, and Safety Groups) into the Health & Safety Excellence program which will guide you not only to develop the health & safety system but also to rebate on premiums and recognition. Let us concentrate on the rebate part.
To understand the rebate process, one needs to understand how this program works and how it is structured.
All businesses with an active WSIB account number (Schedule 1) are eligible for a rebate on WSIB premium through this Excellence program. After attending the info session, a business needs to select a WSIB approved provider to assess its existing system, and choose one to five topics from this program in a year. Then it needs to develop and complete each topic with the help of the provider. After that, the business should submit evidence of the implementation of the completed topic to the WSIB validator to get the rebate on premiums.
The Excellence program consists of three levels: Foundation, Intermediate, and Advanced. These levels contain 10, 17, and 9 topics respectively, a total of 36 topics. The Foundation and Intermediate topics help to accomplish the Plan and Do stages, whereas the Advanced level topics guide to execute the Check and Act steps. The excellence program guideline document also specifically mentions how one can follow the PDCA cycle template to develop these topics. For example, write policies and programs (Plan), communicate, train and implement those (Do), monitor and measure the indicators (Check), and take action for continuous improvement (Act).
A business with 20 per cent or less predictability could receive a 2 per cent rebate, and with more than 20 per cent predictability, could receive a 1.4 per cent rebate of the total annual WSIB premiums per validated topics. However, there are caps on the rebates. The minimum rebate is $1,000 per topic, up to a maximum total rebate of 75 per cent of a businesses’ annual premiums. The maximum rebate is $50,000 per topic.
Hence, an employer could save up to $250,000 in a year and a million dollars in four years by just using the PDCA cycle template, a simple project management tool!
The Binding Force: OHSA
It might be the case that a management system/program standard could miss one or more specific requirements of the Excellence program. Let’s take a very important example.
The OHSAS 18001 misses highlighting the in-depth workers’ participation explicitly, whereas it is a very important aspect of the Excellence program.
Ontario's Occupational Health and Safety Act (OHSA) helps you to accomplish this requisite. How? The Internal Responsibility System (IRS) is one of the core pillars of the act which led to outline the duties of employers, supervisors, workers, constructors, and workplace owners. IRS indicates statutory shared responsibilities of all the parties including workers. Although this term is not specifically mentioned in this act, the Ministry of Labour very often uses this term in its guidelines.
Another important feature of the OHSA, the Joint Health and Safety Committee (JHSC)/Health and Safety Representative (HSR) makes workers’ participation must in workplace health and safety matters.
The same workers’ participation trend is clearly evident with almost all the regulations associated with OHSA. For example R.R.O. 1990, Reg. 851 (Industrial Establishments), section 87.1 directs to consult the committee or the representative during development and implementing the molten martial procedures. O.Reg. 213/91 (Construction Projects), section 17(2) states that the constructor must review the emergency procedures with the committee or the representative of a project.
The final fixture of this bonding is the general duty clause or due diligence clause where OHSA says that employers must take every precaution reasonable in the circumstances for the protection of a worker. And workers’ participation will help to prove the due diligence of any employers.
Hence, OHSA and its regulations always provide various arms and ammunition to counter the risks as well as to develop a system that is in-line with the Excellence program from your existing system.
To summarize the whole discussion, if you have an existing health and safety system, and want to save a lot of money, it’s certainly possible. All you need to do is to take a bird-eye view on your existing programs, and analyze and fit those with the PDCA cycle template, keeping in mind the Excellence program.