Liberty Tire Recycling celebrates five years without a lost time injury at Alberta facility
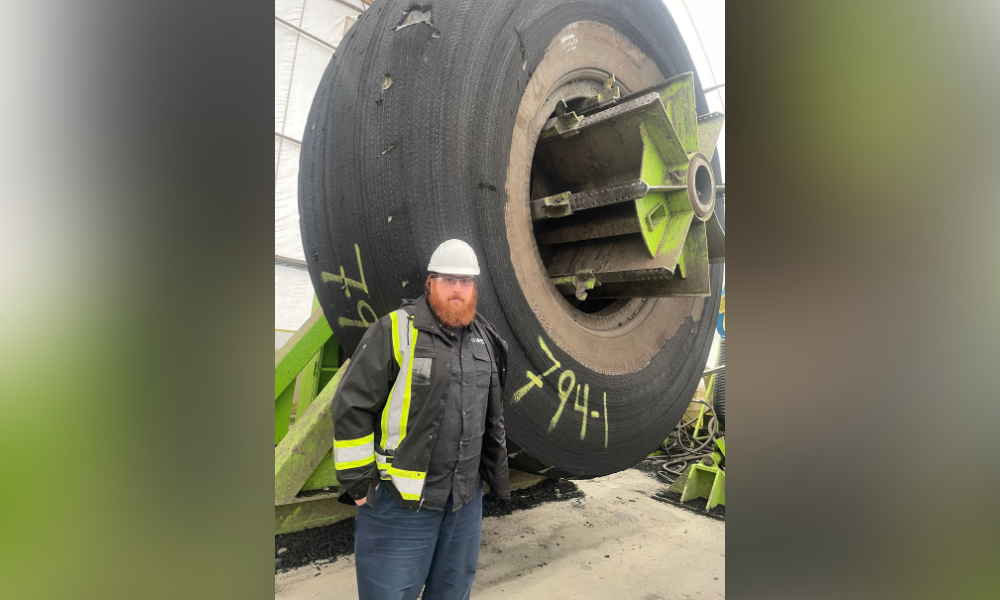
It’s been five years since the team at Liberty Tire Recycling in Alberta experienced a lost time injury and it achieved this milestone by completely revamping its reporting system. Shaun McCabe is the Canadian manager of occupational health and safety and quality control. He says since the overhaul they now have thousands of points of engagement from staff.
“We're at 14,000, last year at 17,000. That's not just the incidents, that's positive engagements, safe work observations, monthly inspections, hazard identification, field level hazard assessments, things like that. There are almost a million points of data that we now can look at.”
When McCabe joined the company in 2015 it had a lost time injury rate of 2.3 and he says the safety culture was good, but not great. "They hadn't had a true health and safety professional working on the team.”
Liberty Tire Recycling takes in all types of tires - from regular commercial vehicles to large industrial trucks used in the oil sands - and turns that rubber in garden mulch or crumb used to create ergonomic mass that can be found in things like speed bumps, playgrounds, and sports fields.
McCabe says the types of injuries workers were experiencing weren’t serious, but they were preventable, “mostly just due to good sprains and strains, you know, muscular, skeletal injury type events.”
Read more: Worker dies in exploding tire accident
Staff didn’t have a standardized method of reporting and recording safety metrics. Over the course of about a year and a half McCabe says they completely revamped the reporting system, “and we started to track everything using spreadsheets, an online application that we still use to this day, to make that reporting easier, but also the tracking of our reactions and our corrective actions and our responses.”
One of the big challenges was getting everybody on the team to buy into the new protocols. But McCabe recalls one moment when the collective light bulb turned on for the entire team. There was a safety issues spotted with piece of heavy equipment and the employees working on it were asked to report it, and then participate in a conversation about how to make improvements.
Read more: New technologies ensure workers not too tired for the job
“That changed everything the moment people saw that we respected their opinion,” says McCabe, “and we took seriously their concern, and we acted on it right away. Engagement probably went up by 50% the following month.”
Now it’s just part of the culture, and McCabe’s efforts are being recognized by senior management within the company. Darcy Rivard is the company’s general manager and says, “with our success at the Alberta facility, we hope to implement similar processes across other locations in North America.”
McCabe’s next task is collaborating with the company’s facility in the Vancouver area. “They have gone 1,000 days without a preventable vehicle accident, they're just about two years without a lost time” says McCabe.
If all goes as planned, that location will mark a five-year milestone too.