Industry insider recommends starting with the basics, and figuring out what is most important
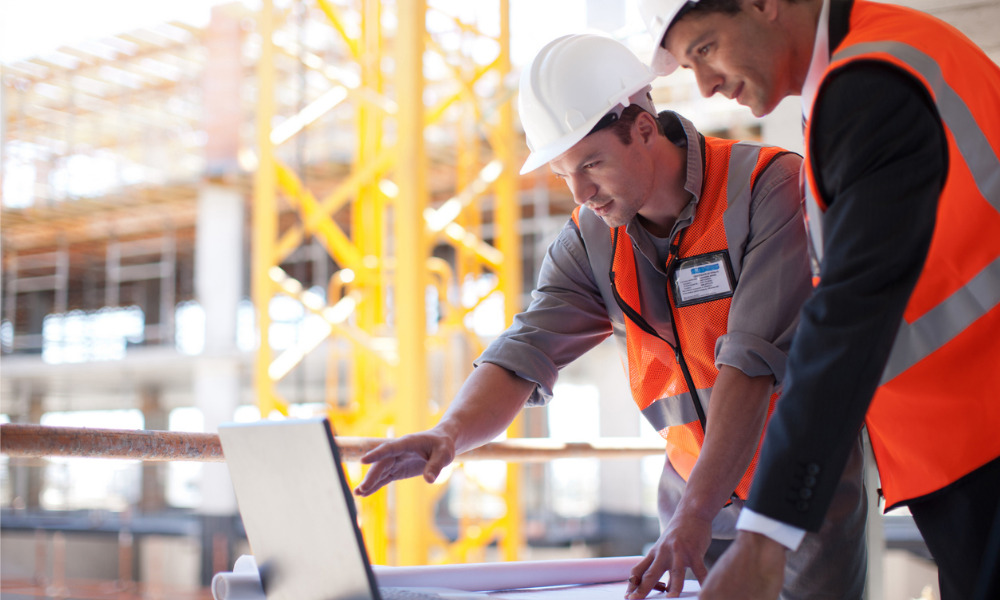
For companies wishing to start or enhance their safety program, it can be a bit difficult to navigate which elements are truly essential to keeping workers safe.
George Minow, Manager of Health, Safety and Wellness, Kitchener-Wilmot Hydro Inc., says that the better way to think about this is which elements of a safety program are the most important, and thus deserve more attention. The answer is to “look at which elements are closest to the actual work being done safely.”
For example, he says that management commitment is a key element to having a quality safety program, “and you definitely want every manager’s and supervisor’s commitment and buy-in to safety".
So while Joint Health and Safety Committees (JHSCs) are legally mandated and invaluable to improving safety, he says that good quality, accessible and appropriate Personal Protective Equipment (PPE) has more of an impact of the safe work that needs to be done, and on the worker culture.
“Making things required for safety more accessible, recognizes that it is more likely that people will work safely if we make it easy for them to do so. What a worker does when no one is around is where your real safety bar is set,” says Minow.
He explains that the key elements to safe work, and those that most affect worker culture include PPE and appropriate vehicles and equipment, employee training which is appropriate to the job and accessible, a good understanding of rules and applicable regulations.
Minow also specifically points to safe work observations (or crew audits), job planning and solid lock out/tag out procedures. On that point, he says that in his industry, “our blue caution tag almost fits in this category or under rules, and we use it if something needs to be communicated about equipment. You can blue tag a chair that needs repair, a hand railing needing repair or a truck that is safe to drive as transportation but it’s equipment cannot be used.”
Though you may not have all the elements mentioned, you can still have a solid safety program because different companies have different needs. It is simply essential that organizations understand what these needs are.
When he and his team were building their organization’s safety program, he says that their core values included having safety “built in.” The organization provides an extensive orientation program “right in the door” which covers risk, managing those risk and their employee rule and handbook which is “filled with lessons learned from injuries and incidents in our industry and company. To continue building this way of life we have all staff attend safety meetings.”
Once his job became big enough to hire more people, they developed a more “formal” safety program which the staff to manage it. “This allowed us to build local expertise readily available to staff. Then we looked to others who had successful safety programs and learned from experts,” says Minow, “so we didn’t stick to only our industry in order to avoid tunnel vision.”
All management staff was trained on the Occupational Health and Safety Act (OHSA) and relevant regulations. “It is more likely we will be in compliance and be safer if we all know our obligations,” says Minow. The team also focused on developing around ergonomics and mental health needs. They also do an external audit of its safety processes every five years to ensure that everything is up to scratch.
Minow says that his team involves and engages the people doing the work “who know it best.” They learn about new safety equipment and better tools from trusted suppliers and equipment shows. Staff bring suggestions of things and methods that make a job safer or more ergonomic.
“We began by and continue to steal with pride programs from others and then adapt them to our company and culture. When you want to start a program look at what has been developed and refined by great safe companies. We learn from each other including new employees who have seen a great thing at another employer,” he says.
For those wishing to make a start, “start with the minimum and ready the regulations that apply to your work,” says Minow. And get help. “If you pay WSIB fees or WCB fees, it is likely you are already paying for expert help with health and safety. They can help you understanding your company’s risk, because they likely know similar companies and then help you know where focus your energy. Most fatalities happen at companies that have never had a serious injury before.”
He also says to be practical. “Don’t wait until a change or solution is perfect to start. Get things going and get feedback to make it better,” says Minow. And “Get to work and find solutions, then check that they are good solutions or if more training or changes are needed.”
“When faced with your list of tasks to do each day, ask which will save a life, a limb or save an injury. Those are the top priority tasks,” says Minow. And safety doesn’t have to negative, far from it. He says to spend of your time on the positive. “Catching your workers doing it right has much more power than fixing an issue being done wrong – which you also have to do. Coach your team to do it right, or least better to start.”
Put in enough effort so that safety can be done at the company without the safety team. “Safety has to happen without you the safety person. You are the coach on the sidelines of the game getting helping the team and quarterback – the supervisor – do the right things.”