Over 42 per cent of Canadians work in noisy environments
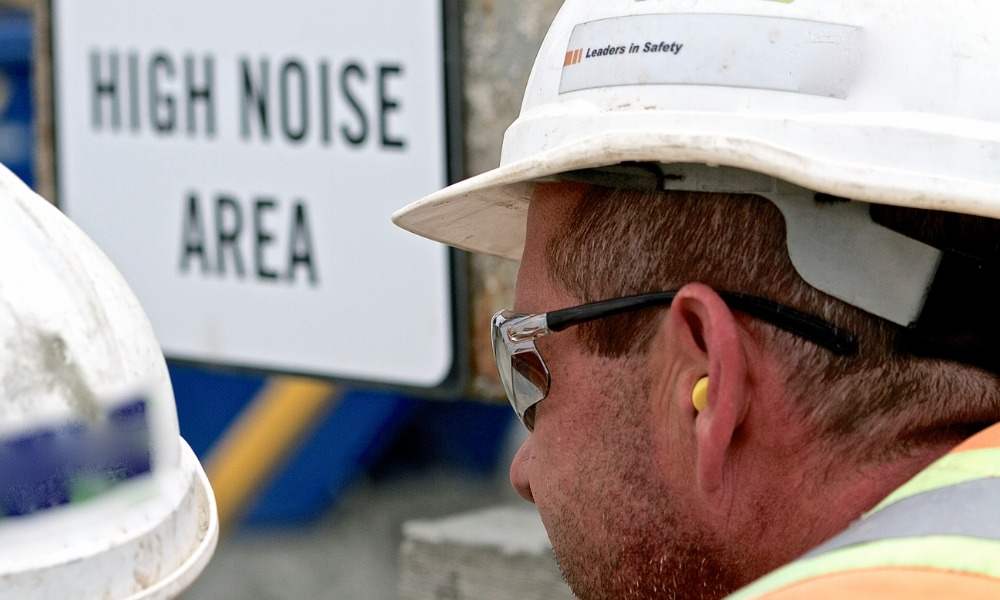
In most sectors, noise is ubiquitous. From loud construction sites to restaurant kitchens, noise exposure is a serious risk in the workplace. In Ontario alone, 30,000 workers between 2006 and 2015 had an allowed noise induced hearing loss (NIHL) claim according to the province’s Workplace Safety and Insurance Board (WSIB).
Statistics Canada estimates that in 2012 and 2013, over 11 million Canadians (42 per cent) worked in noisy environments, or had done so in the past. OHS legislation is supposed to protect workers against dangerous noise exposures, with each jurisdiction defining its own occupational exposure limits (in most provinces, this is around 85 dB of continuous noise over an eight-hour period).
And aside from these occupational exposure limits, what exactly are the safety measures against noise pollution at workplace? Here are six tips on how to reduce noise pollution in the workplace.
Have your machines properly maintained regularly. The top cost effective engineering control to reduce industrial noise hazards is to ensure that all machinery being used in properly maintained, says Graphic Products. For example, machinery where metal on metal contact is present should be inspected and lubricated on a regular basis. This type of maintenance call also extend the life of machinery and prevent unexpected machine failures.
Choose to buy low-noise tools and machinery. While this may be a hefty financial investment, ultimately worker health and safety shouldn’t have a price. There are a number of low-noise tools and machinery available on the market that safety professionals can look into to reduce unnecessary hazardous noise exposures.
Reduce vibration as possible. The Canadian Centre for Occupational Health and Safety (CCOHS) says that employers should limit time spent by workers on vibrating surfaces. In addition, you can put into place controls to mechanically isolate the vibrating source or surface to reduce exposure. Also ensure that equipment is well-maintained to avoid excessive vibration. To further prevent noise, workplaces can also install vibration damping seats, for example.
Enclose or isolate the noise. Safety officers or managers should invest in equipment that can close off loud machines – for example an enclosure with an entrance for workers who need to access that machine. Those working in these enclosures should also have reduced shifts to avoid prolonged exposure to harmful noise levels. If possible, employers should also look into moving noisy machines to more isolated areas of the workplace to further reduce potential harmful exposures.
Try using proper PPE to protect hearing such as earplugs and earmuffs. There are different earplugs and earmuffs available for different sound levels and different concerns. These bits of equipment should be used by any and every worker who is working in potentially hazardous noise environments. Safety professionals should also ensure that this equipment is not cutting workers off from all noise, and workers should still be able to hear their colleagues or their supervisors, and maintain proper communication on site so as not to miss out on key instructions (e.g. if another hazard arises on site). Employers and safety officers should also encourage workers to wear PPE during toolbox meetings, or by posting signage around sites where noise is an issue.
Put a barrier between workers and the noise hazard. Similar to one of the previous points, one of the best ways to reduce noise pollution is to separate the worker from the noise hazard. This could be through the aforementioned enclosures, or other types of barriers that, combined with effective PPE, can reduce the noise hazard.