Green Book 101: What measures must employers take to protect workers? What is a dangerous level of decibels?
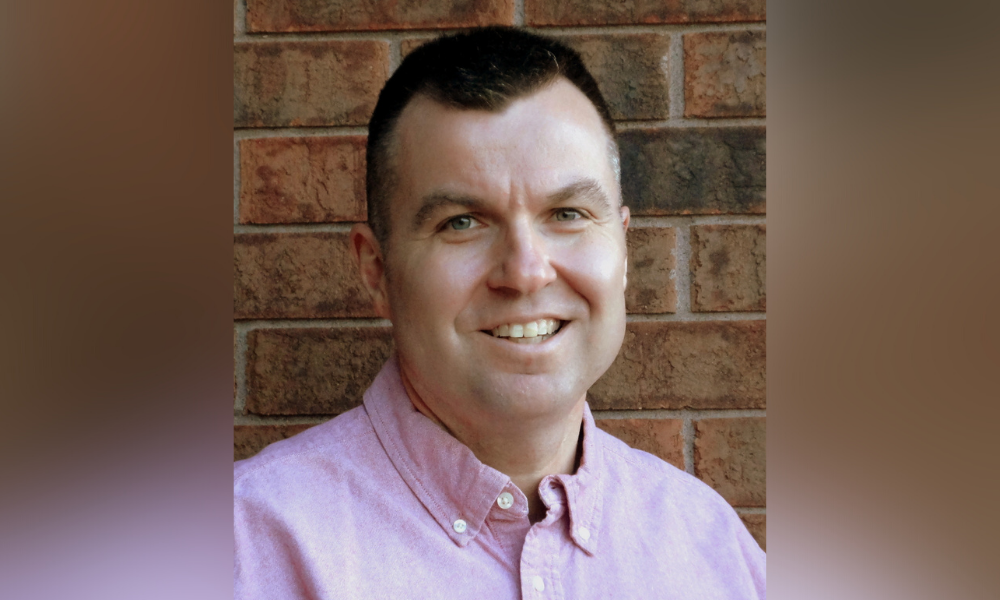
Between 2006 and 2015, around 30,000 workers in Ontario had an allowed noise induced hearing loss (NIHL) claim according to the Workplace Safety and Insurance Board (WSIB). And between 2012 and 2017, 37 per cent of NIHL claims came from the construction and manufacturing industries.
“Industries like mining and construction have very high rates of NIHL since there are a lot of job processes and tools or equipment that have very high sound levels that occur for long durations,” Keith Birnie, Industrial Hygiene and Ventilation Specialist at Workplace Safety North.
Most sectors, however, are concerned. “Noise is ubiquitous," he adds, "it is generally considered a high risk in many industries.” Around 23 per cent of all claims allowed by the WSIB are NIHL claims – a huge chunk, and one which demonstrates just how important it is for employers and safety professionals to understand current regulations.
Loudness and duration
Birnie explains that the loudness (in decibels) and the duration (the length of exposure) are the two main contributing factors to NIHL. The Ontario multi-sector noise Regulation (O. Reg. 381/15) made under the province’s Occupational Health and Safety Act (OHSA) requires that every employer shall ensure that no worker is exposed to a sound level greater than an equivalent sound exposure level of 85 dBA averaged over an 8-hour period.
Permissible exposures under the current regulation do not differentiate between type of noise sources (e.g. continuous, intermittent, impulse). This is why, says Birnie, “it is also important to ensure that you are using the proper noise instruments when doing noise surveys so that you can eventually determine the proper controls by following the hierarchy of controls.”
He says that another way to represent noise is based on daily dose (per cent). For instance, the legislative vale of 85 dBA average over 8 hours is equivalent to 100 per cent dose. If the nose level was 90 dBA you would reach your daily dose of 100 per cent by 2 hours and 32 minutes. “You can see from this that it takes very little increase over 85 dBA to reach your allowable does of 100 per cent,” says Birnie.
In addition, he says that sound levels from noise sources can be considered impulse noise (sometimes referred to as impact noise) such as hammering, or dropping metal on metal. Impulse noise is defined as a single burst of noise with a duration of less than one second. “Research has demonstrated that impulsive noise can cause more severe hearing loss than steady state noise,” says Birnie. It can cause severe hearing loss – even when the overall sound level averages acceptable numbers.
This is why it is so important for employers to be educated on the potential hazards linked to excessive noise levels. But Birnie says that threats can also come from other hazards, such as chemicals. He explains that chemicals which are ototoxic or “ear poisons” can cause damage to the cochlea in the inner ear and/or the auditory neurological pathways. This can lead to hearing loss, tinnitus and vertigo. And sadly, many organic solvents in the workplace are ototoxic.
READ MORE: Why onus is on employers to ensure hazardous materials training
Hierarchy of controls
An Ontario employer, who is covered by the OHSA, has a legal obligation and a general duty to take all measures reasonably necessary in the circumstances to protect workers from exposure to all hazardous sound levels.
In addition to the acceptable levels mentioned above, Birnie says that the legislation “requires that we use the hierarchy of controls,” such as elimination, substitution or engineering, “and not just rely solely on hearing protectors.” He also says that there is a requirement, where practicable, to post clearly visible warning signs at every approach to an area in the workplace where the sound level measured regularly exceeds 85 dBA.
The regulation also clearly states that the employer is required to provide training and instruction to employees on noise hazards, health effects and controls. “An employer who provides a worker with a hearing protection device (HPD) shall provide adequate training and instruction to the worker in the care and use of the device, including its limitations, proper fitting, inspection and maintenance and, if applicable, the cleaning and disinfection of the device,” says Birnie.
And all of these requirements can be put into a formal written hearing conservation program as an integral part of an organization’s broader safety program.
READ MORE: Six critical confined space safety requirements
PPE
There are different forms of personal protective equipment (PPE) available to workers.
The HPDs referenced above include two main types, earplugs and earmuffs. They can be worn alone or in combination. Depending on the activity that the worker is engaging in, employers may want to look for certain models. “You can also get fancy and buy specific types of HPDs that are good for shooting guns, etc. – technology has come a long way,” says Birnie.
He says that for noise levels which range from 85 dBA to 105 dBA, single hearing protection is typically used. When noise levels are above 105 dBA double hearing protection (earplugs with muffs together) is preferred. “Often people do not choose the right HPDs based on the measured sound levels in the workplace. This is why relying solely on PPE can be very ineffective at preventing NIHL,” says Birnie.
Broadly, Birnie says that as with many other hazards, employers and safety professionals should always strive to follow the hierarchy of controls and not rely solely on PPE.