WorkSafeBC fines company $68K, says worker had not been properly trained for confined space work and there were deficiencies in procedures
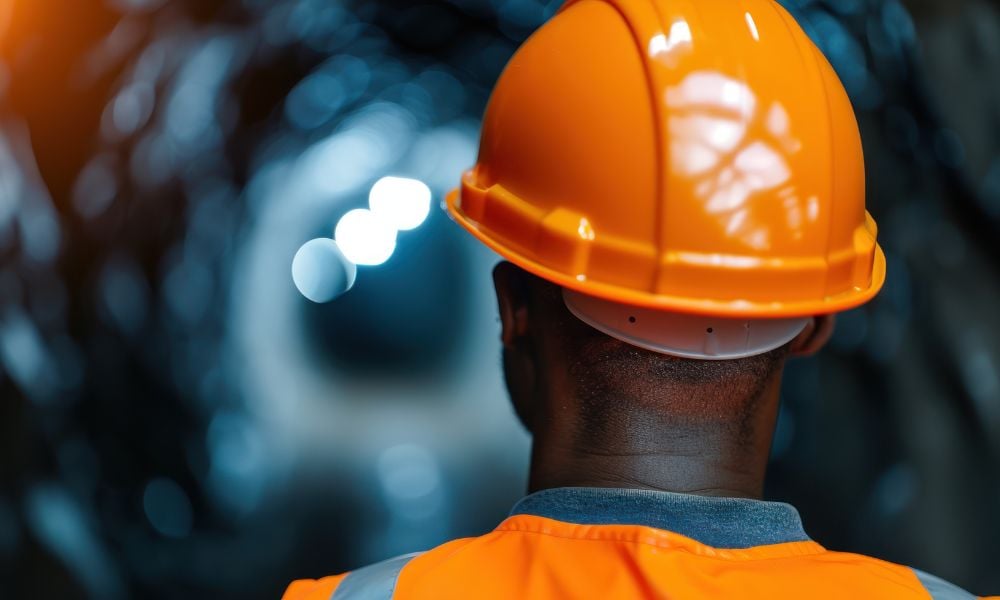
British Columbia employer Lane Construction Services Ltd. has been fined $68,479.59 for numerous safety violations.
The infractions occurred while the company was performing concrete forming work at an apartment complex construction site in North Vancouver.
One worker, assigned as the standby person for confined space work in a below-ground stormwater tank, fell approximately 4.3 metres (14 feet) through an unsecured floor opening into the tank.
WorkSafeBC determined that while the worker had been wearing fall protection, they had not been provided with a lanyard or an anchor point.
Also, the worker had not been properly trained for confined space work, and there were deficiencies with the firm's confined space entry procedures, according to the government agency.
“The firm failed to ensure a ventilation system to control airborne contaminants in a confined space was installed and maintained according to engineering principles, and failed to ensure it conducted atmospheric testing before a worker entered a confined space,” said WorkSafeBC.
“The firm failed to ensure fall protection was used, a repeated violation, and failed to ensure floor openings accessible to workers were securely covered or guarded. In addition, the firm failed to ensure the health and safety of all workers at its worksite. These were all high-risk violations.”
Worker safety in confined spaces
Ensuring worker safety in confined spaces is a critical responsibility for employers, particularly given the high-risk nature of such environments. WorkSafeBC provides clear regulatory requirements and best practices under Part 9 – Confined Spaces of the Occupational Health and Safety Regulation (OHSR). Here’s a summary of key steps employers must take, directly aligned with WorkSafeBC guidelines:
1. Conduct a confined space hazard assessment. Before any entry, employers must conduct a written hazard assessment of the confined space to identify all potential hazards, including:
- Toxic or oxygen-deficient atmospheres
- Engulfment or entrapment risks
- Mechanical, electrical, or process hazards
“The employer must ensure that a hazard assessment is conducted for each confined space to determine the hazards that may be present.” — WorkSafeBC, OHSR 9.9
2. Develop and implement a confined space entry program. Based on the hazard assessment, employers must create a written confined space entry program. This must include:
- Safe work procedures
- Identification of roles and responsibilities (entry supervisor, standby person, entrant)
- Equipment and PPE requirements
- Emergency rescue plans
“A written confined space entry program must be implemented by the employer and must address all procedures, equipment, training, and responsibilities necessary for safe entry.” — WorkSafeBC, OHSR 9.10
3. Ensure atmospheric testing and ventilation. Employers must ensure that air testing is done before and during entry to monitor for oxygen levels, toxic gases, or flammable substances. If needed, ventilation systems must be used to maintain safe atmospheric conditions.
“Before a worker enters a confined space, the atmosphere must be tested and continuously monitored if a hazardous atmosphere could develop.” — WorkSafeBC, OHSR 9.18 & 9.19
4. Provide proper training and supervision. All workers involved in confined space work must receive confined space entry training, including hazard recognition, use of PPE, and emergency procedures. A qualified person must supervise entry operations.
“Each worker who enters a confined space must be adequately trained in the hazards, procedures, and use of protective equipment.” — WorkSafeBC, OHSR 9.34
5. Establish emergency rescue procedures. A rescue plan must be in place and practiced, including:
- Methods of rescue
- Availability of rescue personnel and equipment
- Communication systems
“A plan for the rescue of workers must be developed, implemented, and communicated to all affected workers.” — WorkSafeBC, OHSR 9.36