Over one quarter of work injuries are to the hand
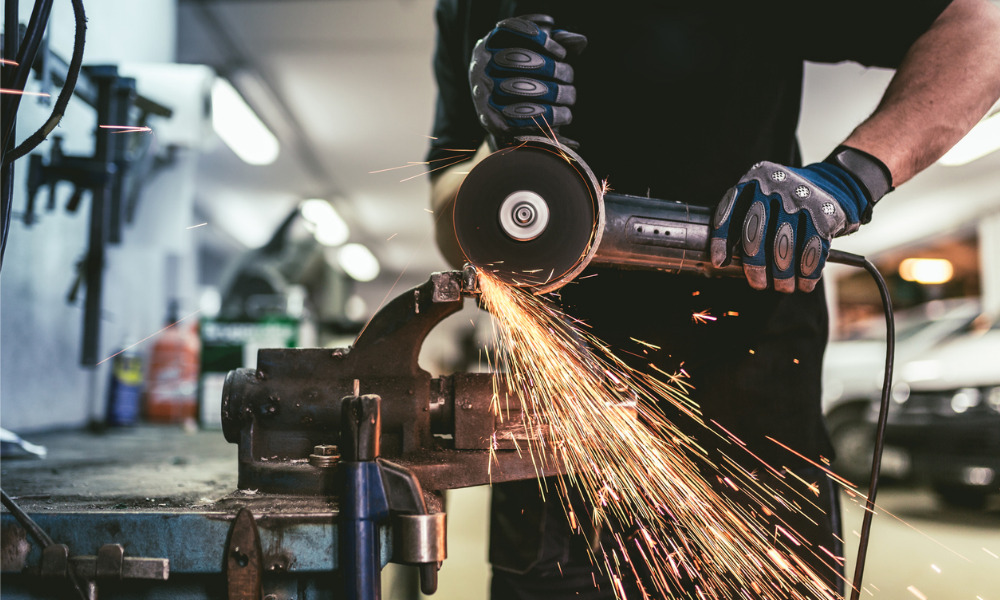
Hand injuries are among the most common at work. A 2003 report from Statistics Canada indicated that the hand was the most frequently injured body part on the job – over one quarter (28 per cent) of work injuries are to the hand.
More recent data from Statistics Canada indicates that the most common types of injuries sustained at work are sprains and strains (49.9 per cent), followed by cuts, punctures or bites (19.2 per cent) and then broken or fractured bones (8.7 per cent). These are all injuries that can affect workers’ hands.
It makes sense – workers in all occupations use their hands in some way, from office workers tapping away at keyboards to warehouse workers carrying and lifting heavy objects. With these limbs at risk, there are a number of things that employers and safety officers and managers can do to enhance safety and protect workers’ hands.
1. Invest in the right PPE. Of course, gloves are the probably the most important bit of protective equipment that workers can wear to protect their hands. There are different types of gloves available on the market for different types of occupations. Indeed, different hazards call for different materials. Leather or canvas gloves can be used to protect against cuts, burns or punctures. Lead-lined gloves are used to protect against ionizing radiations. Insulated rubber gloves can protect against electrical hazards. Employers should look into which gloves are the most suitable for their workers. If you're looking for gloves to protect your workers from cuts to their hands, read the best cut-resistant gloves here.
Hand and arm protection is not limited to gloves; protective sleeves or coverings, finger guards and even barrier creams can be used by workers to protect their precious limbs.
Read more: Everything you need to know about hand protection
2. Implement ergonomic solutions. Musculoskeletal disorders (MSDs) are a huge risk for workers across the board. Hands are particularly at risk. For example, office workers or those working from home may not have the right equipment – keyboards, mice, desks that are too low, etc. Improper equipment can have lasting consequences, such as carpal tunnel syndrome. Doing research and consulting with an ergonomist can empower employers and safety professionals to invest in the right ergonomic equipment to prevent the development of MSDs.
Read more: Workplace ergonomics: Four key things to consider
3. Communicate with workers. As with any workplace issue, one of the best things that employers and safety professionals can do is actually consult with their workers on what they need. Perhaps workers aren’t being provided with the correct gloves, or the equipment provided isn’t comfortable or intuitive to use. Certain tasks may not seem to pose a hazard, but they may be causing a worker harm in the immediate or long-term. Keeping open channels of communication with workers is always a must.
4. Training and education. Providing the right tools and equipment is great, but if workers aren’t trained on how to properly use them then the hazard remains. Workers also need to be educated on the hazards posed to their hands, with reminders about the serious consequences that can occur if hand safety protocols are not be properly respected. As with any bit of training, refresher courses are always useful.
5. Ensure adequate machine safeguarding solutions. Workers getting their hands or legs caught in machinery at work is sadly more common than you think. Hands getting pinched, cut, or caught up in a machine is a serious workplace hazard and workplaces must ensure that they are compliant with safety regulations. Serious consequences can include crushed hands or fingers, amputations and even fatalities. These hazards should be identified during a workplace risk assessment, and control and prevention measures should be put into place to ensure that workers are not exposed to these unnecessary hazards.
Read more: Best practices for conducting workplace risk assessment